Galvanized welded mesh panels have emerged as a quintessential building material in the construction and agricultural sectors, owing to their unparalleled strength, durability, and versatility. What makes these panels particularly noteworthy is the galvanization process, which involves coating them with a protective layer of zinc. This layer is crucial in enhancing their resistance to rust and corrosion, making them suitable for use in various environments and climates.
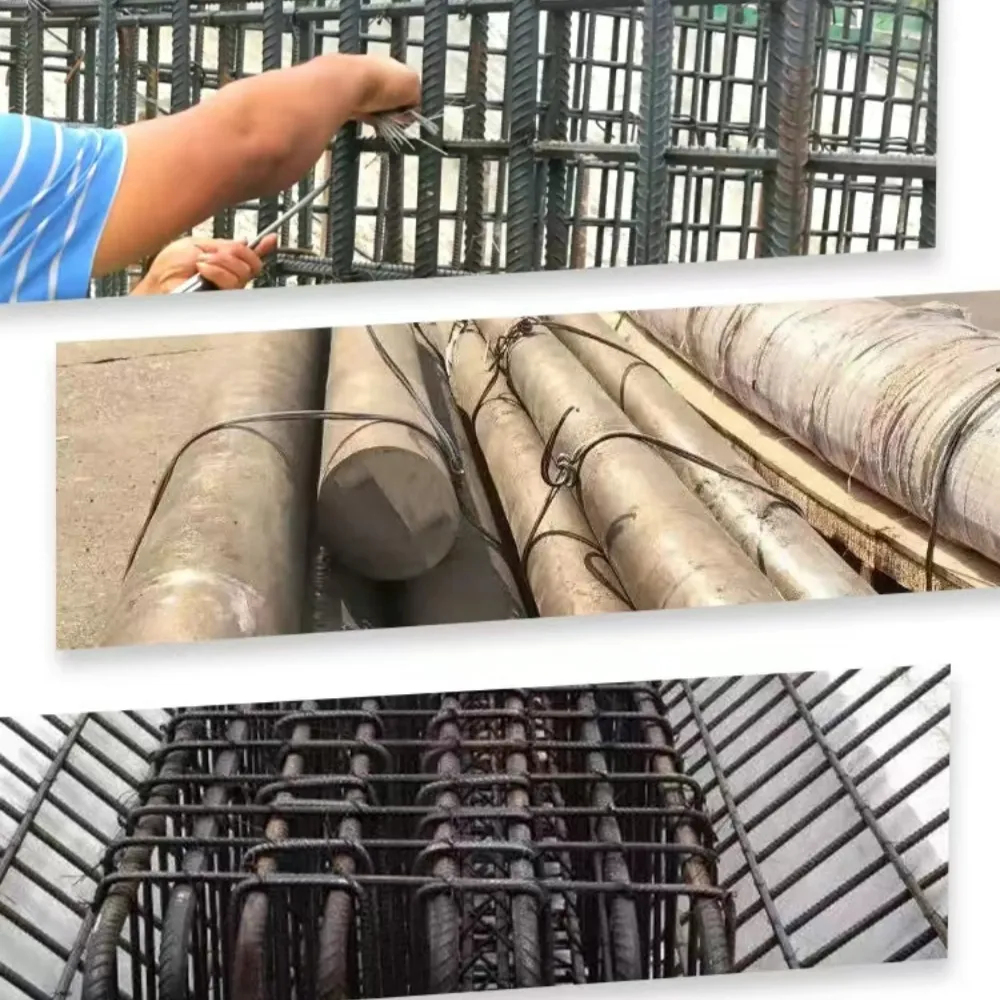
From my extensive experience as an SEO specialist deeply involved in the construction industry, I have witnessed firsthand the transformative impact of galvanized welded mesh panels in modern building practices. Their robustness is not only theoretical but is grounded in numerous practical applications. For instance, these mesh panels are extensively used in reinforcing concrete in infrastructure projects, thanks to their ability to withstand high tensile stress without succumbing to environmental degradation.
Furthermore, their inherent strength does not come at the cost of flexibility. Galvanized welded mesh panels can be customized to fit specific architectural designs, which is why they are a favorite among architects and builders aiming for both aesthetic appeal and structural integrity. The panels can be easily cut and bent to suit a myriad of design and structural requirements, providing an unrivaled balance between form and function.
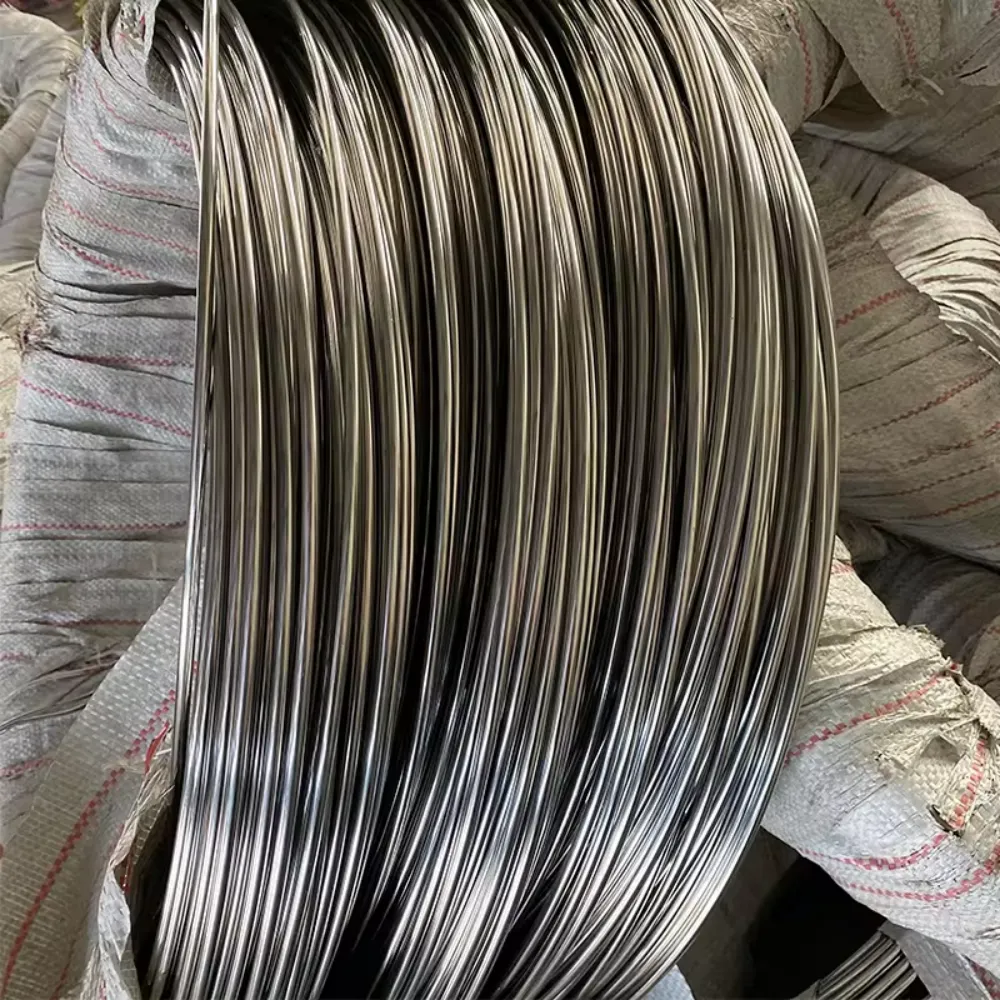
Delving into the technical expertise of galvanized welded mesh panels, the galvanization process is crucial. Through hot-dip galvanization,
wherein the welded mesh is submerged in molten zinc, each panel gains a protective layer that significantly boosts its longevity. Not only does this protect against physical wear and tear, but it also provides a formidable defense against corrosive elements. This ensures that structures utilizing these panels maintain their integrity for decades, reducing the need for frequent maintenance and replacement—a crucial factor for cost savings in extensive projects.
galvanized welded mesh panel
Authoritative sources in the construction sector, including leading engineering journals and building code guidelines, consistently advocate for the use of galvanized welded mesh panels in a range of applications. From perimeter fencing in high-security zones to livestock enclosures in agricultural settings, their endorsement is grounded in studies proving the panels' ability to maintain rigidity and structure under pressure. Their consistent performance in these applications lends a level of trust that is invaluable for project managers and engineers who must adhere to tight deadlines and budgets.
Trustworthiness is another key attribute of galvanized welded mesh panels. Unlike traditional wood or lesser-grade metals that may falter over time, these panels offer peace of mind with their low maintenance requirements. Having worked closely with contractors over the years, feedback is overwhelmingly positive; projects employing these panels report not only fewer structural issues but also a significant reduction in long-term operational costs. Clients appreciate the confidence these panels instill, knowing that their investments are protected against the unpredictable whims of nature and time.
In conclusion, choosing galvanized welded mesh panels is about investing in a material that promises reliability and efficiency. It is a decision backed by experience, endorsed by industry expertise, validated by authoritative research, and trusted by countless professionals. Whether in a high-rise urban development or a rural agricultural setting, these panels provide a steadfast solution, embodying the principles of sustainability and practicality in modern construction. Their versatile application and resilient nature make them an indispensable asset in any project aimed at achieving excellence in durability and performance.