Understanding the cost of welded wire fabric is pivotal for project planners, cost estimators, and construction managers. Welded wire fabric (WWF), recognized for its strength and versatility, is extensively utilized in various sectors including construction, landscaping, and agriculture. This article seeks to explore the multiple dimensions influencing the cost of welded wire fabric while weaving in real-life experiences, expert insights, and industry standards, ensuring a trustworthy and authoritative guide.
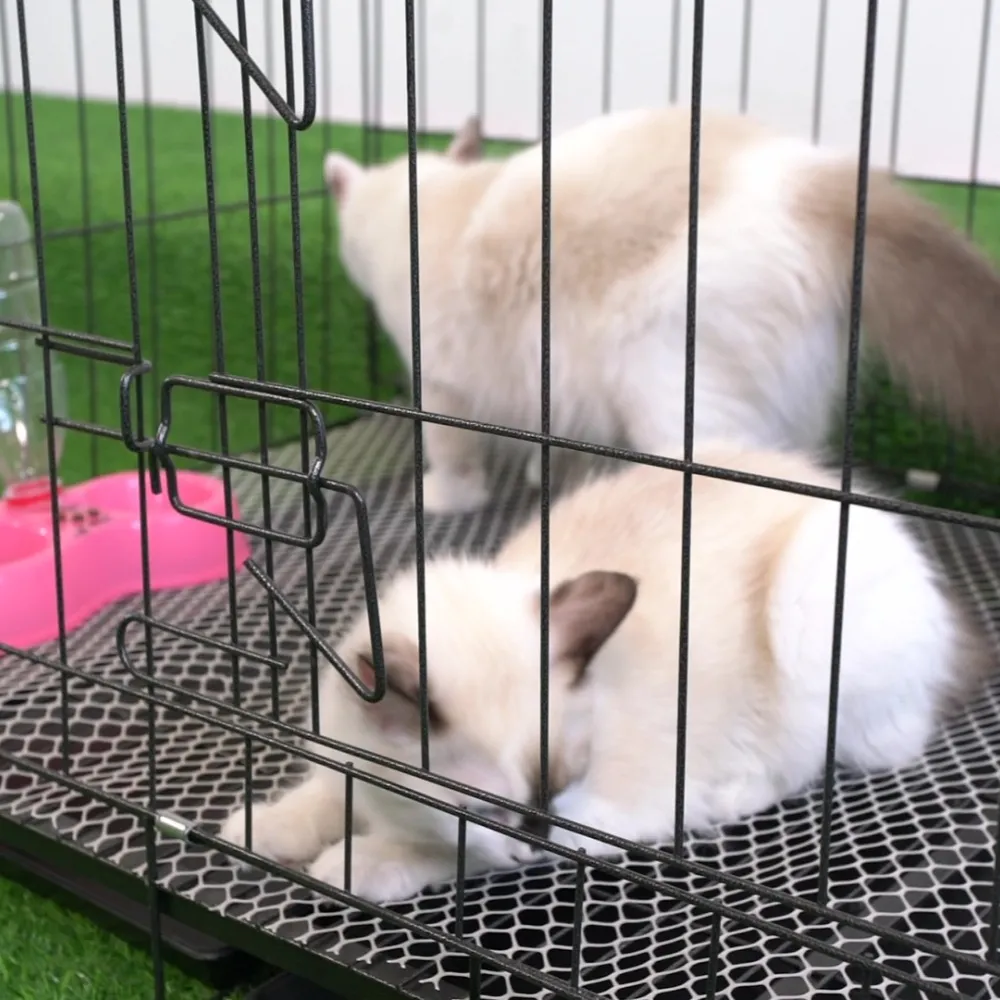
Key Factors Affecting the Cost of Welded Wire Fabric
1. Material Composition
The choice between stainless steel, galvanized steel, or plain carbon steel significantly impacts cost. Stainless steel, with its superior rust resistance and durability, often commands a premium price. Galvanized steel provides a balance between cost and corrosion resistance, suitable for outdoor applications.
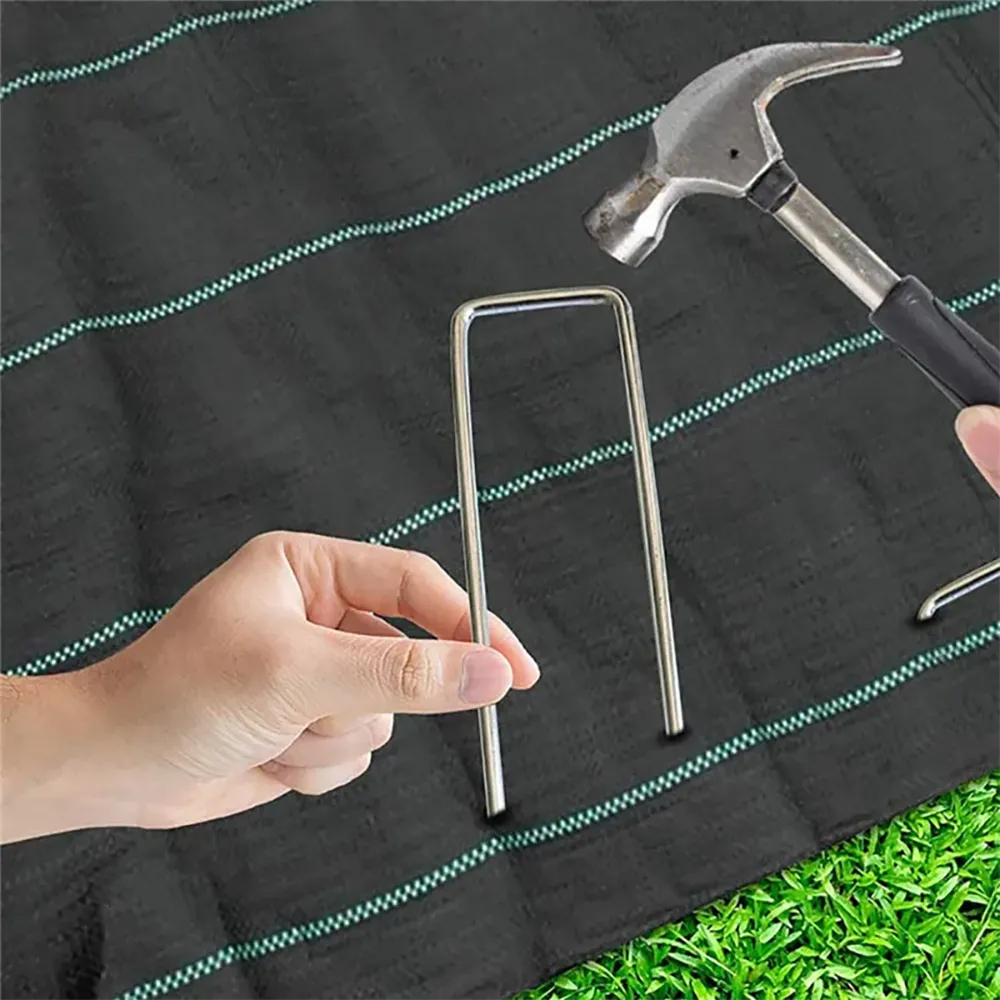
2. Mesh Size and Wire Diameter
The cost is directly proportional to the mesh size and wire diameter. Finer mesh with thicker wires typically increases the price due to increased material usage and more complex manufacturing processes. For instance, 4x4-inch mesh with a heavier gauge will be more expensive than a 6x6-inch mesh with a lighter gauge, suiting simpler applications.
3. Manufacturing Process
Advanced manufacturing technologies such as automated welding and coating processes can reduce production time, yet introduce additional cost due to technological investment. However, these technologies ensure consistent quality and reduce human error, which might justify the upfront expense.
4. Regional Availability
Proximity to manufacturing facilities or suppliers can significantly affect shipping costs. Areas with limited access to raw materials or production facilities may experience higher costs due to transportation.
5. Project Volume and Specifications
Large projects that order WWF in bulk often benefit from discounted pricing. Specialized requirements such as custom dimensions or coatings can add to production costs, affecting overall pricing.
cost of welded wire fabric
Real-Life Experiences and Insights
In the words of a construction manager involved in high-rise building projects, Selecting the appropriate welded wire fabric is crucial not just for cost management but also for ensuring the structural integrity of our projects. We've observed a noticeable cost variation when ordering custom-sized mesh versus standard sizes. Planning ahead and consulting with suppliers on lead times and standardized products have saved us significant costs and headaches.
Industry Expertise and Authoritative Guidance
According to industry experts, adopting a strategic approach when sourcing WWF is essential. Engaging with suppliers during the early planning phase allows for better negotiations on pricing and understanding market dynamics that can affect cost. Experts suggest exploring options such as strategic stocking or partnering with reliable suppliers to mitigate cost volatility.
Trust and Credibility in Supplier Selection
Choosing reputable suppliers enhances trustworthiness and ensures that the WWF meets industry standards. Certification and adherence to ASTM or other local standards verifies the quality and safety of the product. It's advisable to request detailed product specifications and certifications from potential suppliers to avoid substandard materials that could compromise project quality and safety.
In summary, navigating the complexities of welded wire fabric pricing requires a comprehensive understanding of material properties, manufacturing processes, and market conditions. By leveraging expertise, gathering real-world insights, and prioritizing authority and trust, project stakeholders can make informed decisions that optimize both quality and cost-efficiency. Balancing these elements facilitates successful project outcomes, setting a strong foundation for sustainable and resilient construction practices.