Iron nail manufacturing is an intricate industry combining technology, precision, and quality control, ensuring that each nail produced meets exacting standards for various applications. The detailed process from raw material to finished product involves expertise, meticulousness, and innovation, appealing to both industry specialists and general consumers.
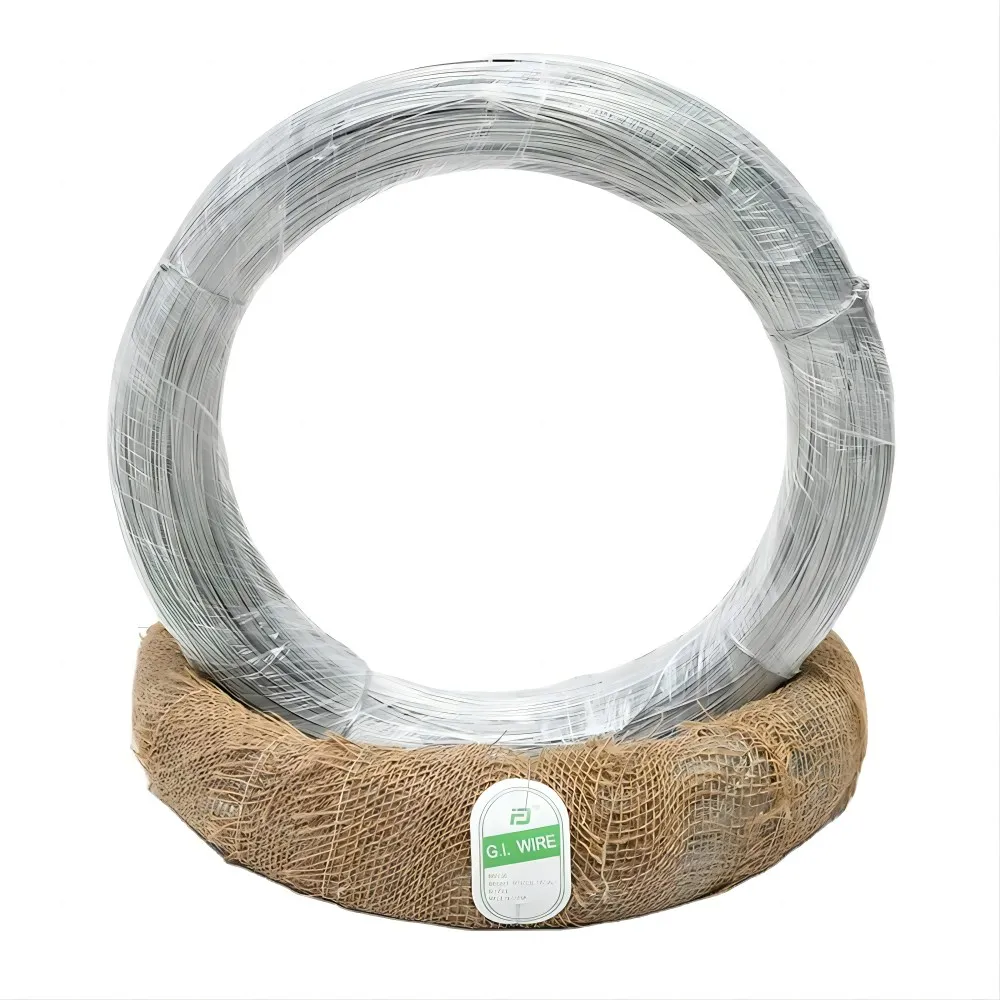
Expertise plays a crucial role in iron nail manufacturing. The process begins with the careful selection of raw materials, primarily low-carbon steel wire, known for its ideal balance between strength and malleability. This initial stage requires a deep understanding of material science to ensure the selected iron wire meets industry durability standards for its end applications, whether for construction, carpentry, or even artistic works.
An essential aspect of manufacturing is the drawing process, where iron wire is pulled through a series of dies, progressively reducing its diameter. This step demands precision engineering, as the gauge of the iron wire directly affects the final nail size and its performance under stress. Each step in this stage is controlled by a mix of automated and manual adjustments, requiring skilled technicians to ensure consistency and quality control.
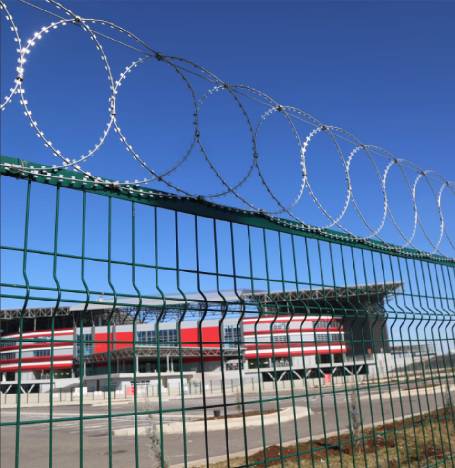
The cut and point phase follows, where iron wire segments are cut to the desired length, and machine presses shape one end into a point. This phase is particularly reliant on cutting-edge machinery that combines speed with accuracy. Operators must maintain uniformity and precision, as any deviation may render the nails ineffective or cause them to structurally fail under applied loads.
In addition to the point,
iron nails may feature different head shapes depending on their intended use. This stage, known as heading, employs machines that stamp the opposite end of the nail into varying head forms, such as flat, conical, or countersink styles. Expertise in this stage involves understanding mechanical force dynamics as well as attention to detail, which ensures the correct formation of head shapes and offsets potentials for user error during nail application.
iron nail manufacturing
Post-fabrication treatments comprise surface finishing processes, such as galvanization, which coats the nails in zinc to enhance resistance to rust and corrosion. Plating and polishing demand comprehensive knowledge of chemical processes and environmental standards, underscoring the manufacturer’s commitment to producing viable, long-lasting products. This expertise not only enhances nail longevity but also contributes to sustainability by reducing waste.
Quality control and testing are pivotal throughout production. A stringent system of checks, including visual inspections and tensile strength testing, ensures these nails consistently meet rigorous quality benchmarks. Each product is carefully assessed for structural integrity, durability, and compliance with national and international standards.
The scale and scope of production operations, from small batches for bespoke orders to large-scale manufacturing, highlight the industry's flexibility and adaptability. Authoritativeness in the field is showcased by manufacturers who leverage ISO certifications and compliance with ASTM (American Society for Testing and Materials) specifications, reifying their nails' quality assurance.
Trustworthiness and reliability hinge on transparent business practices, warranty offerings, and quality guarantees. Manufacturers fortify client trust by offering warranties and detailed product information, reinforcing consumer confidence in the iron nails’ performance and longevity.
In conclusion, the iron nail manufacturing industry exemplifies a blend of traditional expertise and modern technological advancements. Its success is grounded in the precision and consistency of its production processes, strict adherence to quality standards, and dedication to delivering a product that professionals and consumers alike can rely on. From material selection to finishing touches, each stage enriches the nail’s lifecycle, embodying a commitment to excellence and the continuous pursuit of innovation in manufacturing practices.