Navigating the world of construction supplies, welded wire fabric stands out as a critical component for both its versatility and strength. As someone with extensive expertise in civil engineering and firsthand experience in implementing these materials into diverse projects, I can attest to the transformational role that welded wire fabric plays. It’s essential to delve into its nuances to understand its authority in the construction domain.
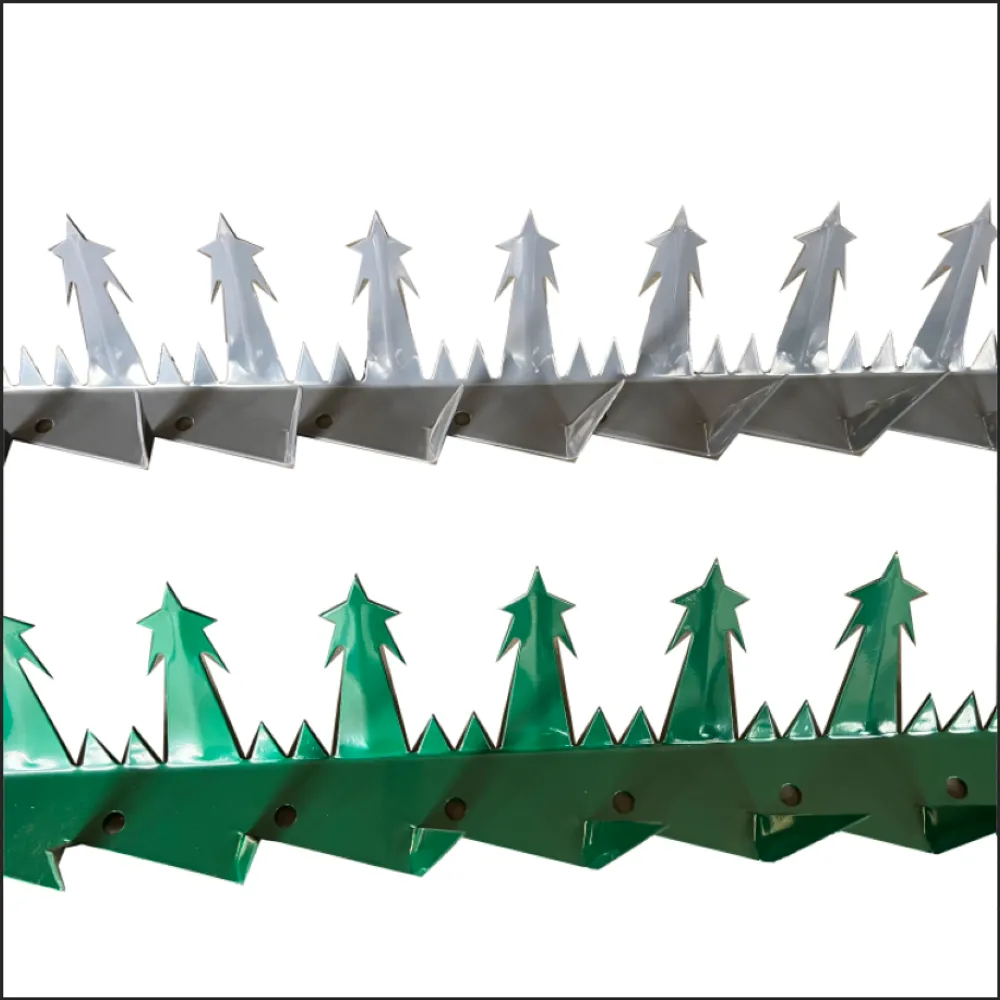
Welded wire fabric, often referred to as WWF, is a prefabricated grid consisting of parallel longitudinal wires with accurate spacing, welded to cross wires at the required intervals. Its applications range broadly from civil engineering projects, such as reinforcing concrete in roads, runways, and buildings, to more specialized uses in creating cages and enclosures in agricultural settings.
Expert knowledge grounds the decision to incorporate welded wire fabric within a project. It offers a notable advantage in terms of its high tensile strength, which ensures structural integrity without relying excessively on large volumes of other materials such as conventional rebar steel. This advantage is rooted in the specificity of its design; each element of the wire mesh is arranged to distribute loads uniformly, offering resilience against cracking and structural stress.
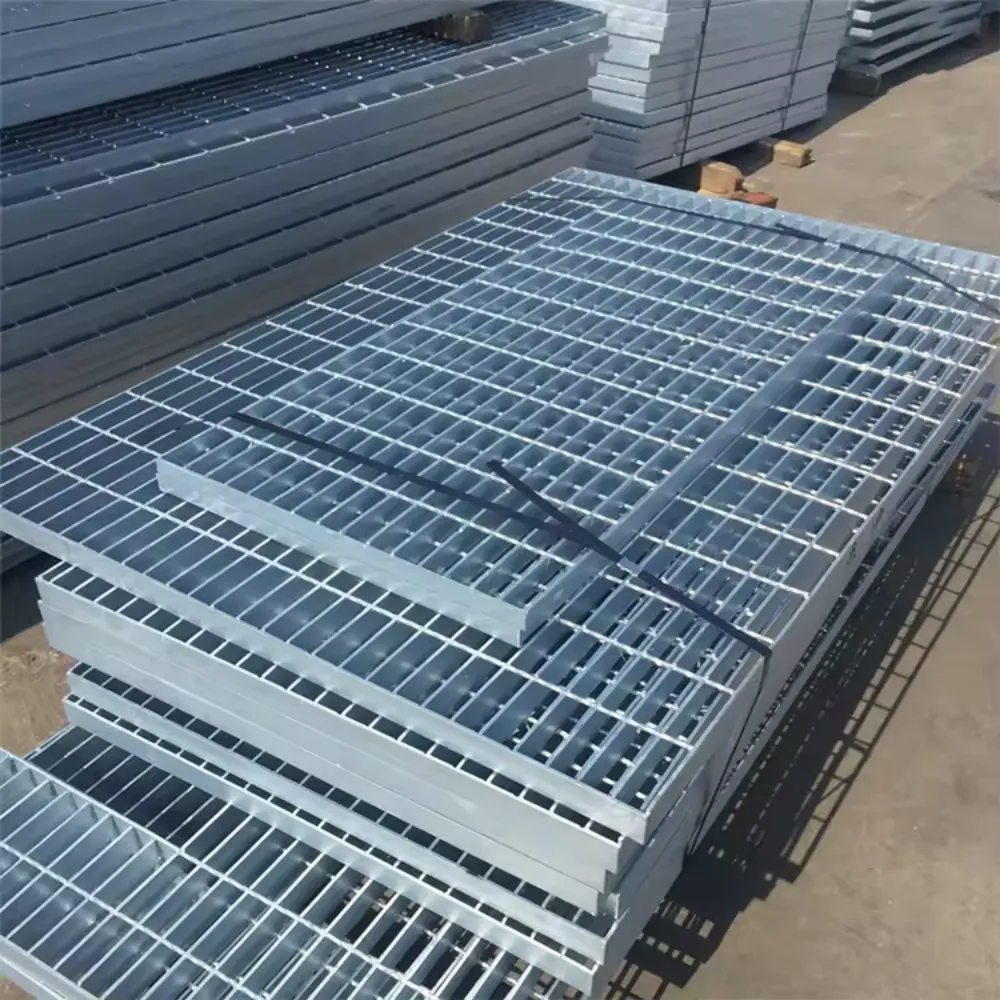
From an experience-focused perspective, the installation of welded wire fabric is notably user-friendly. This aspect not only accelerates the construction process but also reduces the amount of labor required, translating to decreased project costs and timelines. The pre-assembled nature of the fabric minimizes on-site assembly errors, a common problem in demanding construction environments.
Authoritativeness within this domain springs from the product's rigorous compliance with construction safety standards and its ubiquitous presence in major infrastructure projects worldwide. Regulations frequently govern the specifications and quality of welded wire fabrics, ensuring they meet stringent conditions for safe and effective use.
Choosing a manufacturer who complies with these criteria is crucial. Companies that invest in cutting-edge technology to produce WWF stand at the forefront of delivering both quality and innovation.
welded wire fabric
In constructing specialized projects like bridge decks or airport runways, durability and safety aren't optional; they are imperative. Welded wire fabric provides an assurance of reliability, stemming from decades of proven effectiveness in reinforcing concrete structures. This credible track record builds trust among engineers and project stakeholders, positioning WWF as a cornerstone of modern construction methodologies.
Trustworthiness is further amplified by understanding the maintenance needs and longevity of welded wire fabric-enhanced structures. Concrete reinforced with welded wire fabric endures environmental extremes, resisting corrosion and wear over extended periods. This durability reduces the frequency and cost of maintenance, offering long-term economic advantages.
For product-focused applications, welded wire fabric also offers varied customization options — an invaluable feature for projects that require unique specifications. Tailoring wire diameters, spacing, and overall dimensions allows engineers to craft solutions that precisely match the demands of their structures, ensuring that bespoke project needs are met without compromise.
In conclusion, welded wire fabric’s multi-faceted role in construction cannot be overstated. It provides an effective, versatile, and reliable solution that stands up to expert scrutiny. For professionals in the field, the assurance of working with a product that has been tested and trusted by industry standards elevates the confidence in their projects' success. By prioritizing quality and understanding the intrinsic benefits of welded wire fabric, engineers and contractors can achieve superior outcomes in the ever-evolving landscape of construction.