When seeking robust and reliable solutions for galvanization needs, hot-dip galvanized iron (GI) wire stands out as a premium choice among manufacturers worldwide. This article delves into the essential aspects of hot dip GI wire manufacturing, demonstrating expertise in the field, and showcasing authoritative knowledge that customers can trust.
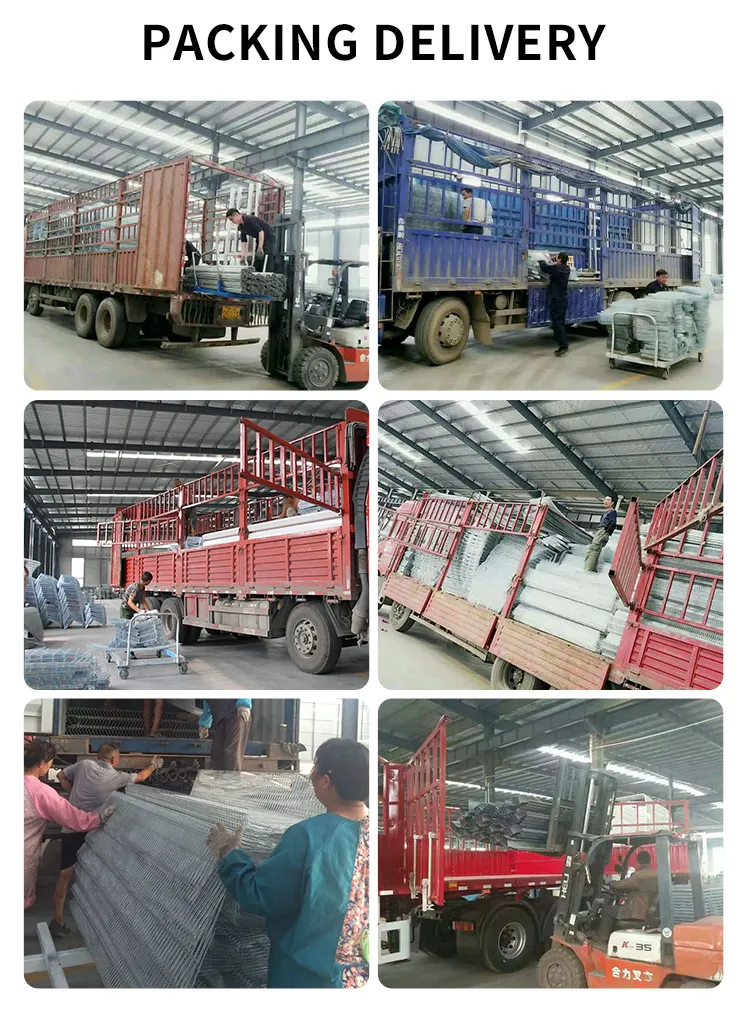
Hot dip GI wire, known for its corrosion resistance and durability, is integral to industries ranging from agriculture to construction. The process of manufacturing hot dip GI wire begins with selecting high-quality raw steel wire. This selection lays the foundation for the entire production, emphasizing the importance of expertise in material selection to ensure the final product meets stringent quality benchmarks.
An authoritative approach to the production process involves meticulously threading the steel wire through a series of steps including cleaning, annealing, and coating. Cleaning the wire thoroughly removes impurities that could interfere with the galvanizing process. This is achieved through a combination of degreasing baths, acid solutions, and water rinses, underscoring the manufacturer's commitment to producing uncompromised products.
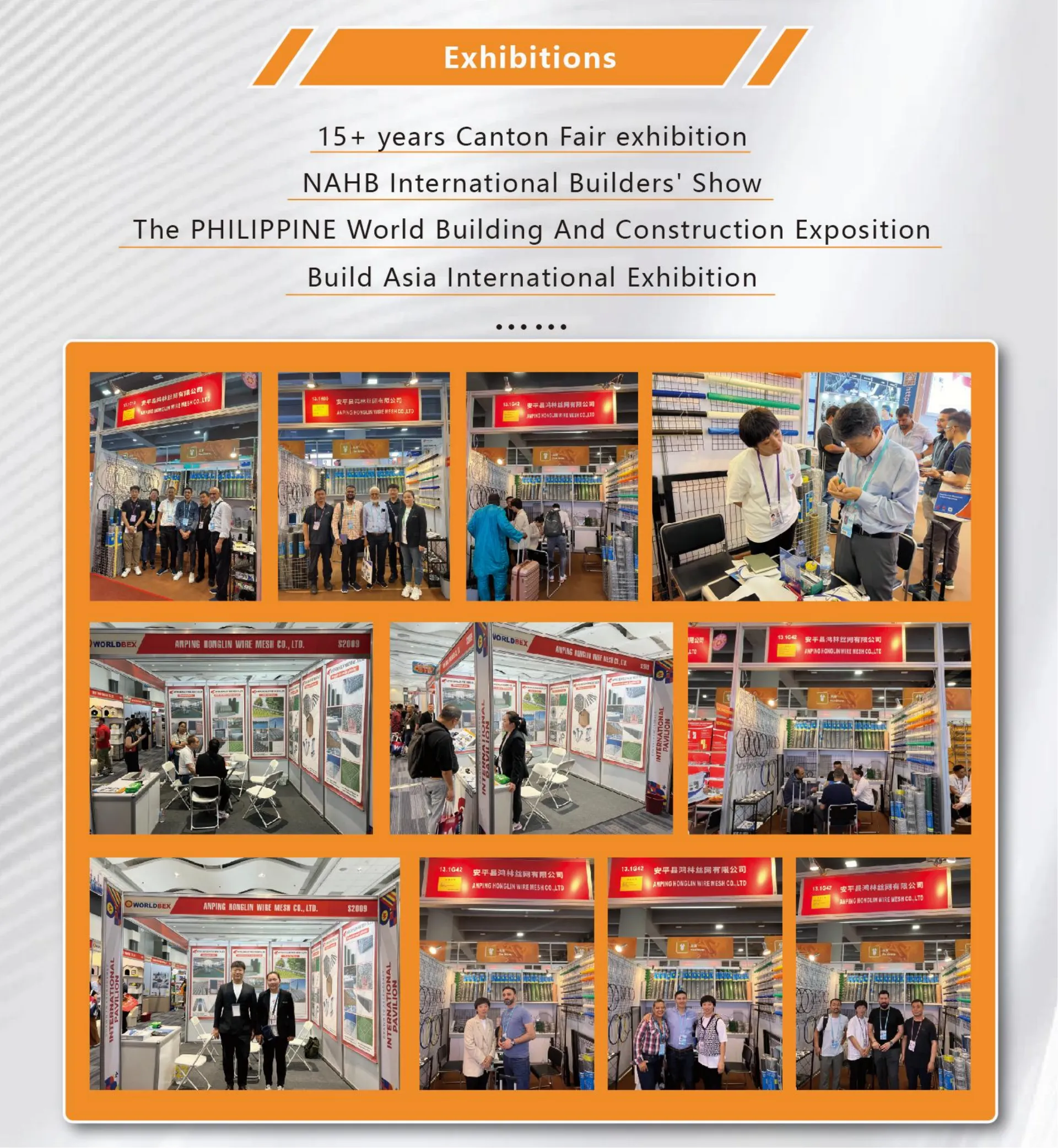
Annealing, another critical step, involves heating the wire to a specific temperature to alter its properties for improved pliability and strength. Expertise in achieving the optimal balance between temperature and duration is crucial here, ensuring the wire does not lose its inherent toughness while gaining flexibility.
The final stage, the hot-dip galvanizing process itself, involves immersing the wire in a bath of molten zinc for a set period.
This step requires detailed attention and accuracy. The manufacturer's skill in controlling bath temperature and zinc composition directly affects coating thickness and uniformity, which are significant factors for long-term performance.
Among the leading manufacturers, quality control is not optional; it is essential. Comprehensive testing protocols, such as tensile, torsion, and coating thickness tests, are implemented to verify the product's durability and performance under varying conditions. These manufacturers stand out due to their rigorous inspection regimes and capacity to deliver consistent quality, which builds trust with their clients.
hot dip gi wire manufacturers
In addition to technical prowess, authoritative manufacturers uphold environmental standards and adhere to sustainable practices, emphasizing trust and accountability. This includes responsible sourcing of materials, recycling of waste generated during production, and limiting emissions to lower the overall environmental footprint.
True authority in the hot dip GI wire industry is also displayed through continuous innovation. Industry leaders are investing in research and development to enhance galvanization techniques, reduce costs, and further improve the wire's protective properties. Manufacturers committed to innovation are more than suppliers; they are partners in progress, helping industries adapt to evolving challenges.
Recent advances in automated technology and digital monitoring systems are becoming commonplace in manufacturing facilities. These innovations increase precision, reduce human error, and optimize processes. Expert manufacturers leverage these technologies to offer competitive pricing while maintaining superior quality, reflecting their command over modern industrial practices.
Hot dip GI wire manufacturers are not merely providers of materials; they are indispensable partners in industrial development. Their expertise, commitment to quality, adherence to regulatory standards, and investment in eco-friendly practices make them trustworthy and authoritative additions to any project requiring durable wire solutions.
Ultimately, when choosing a hot dip GI wire manufacturer, look for the hallmarks of experience and expertise, a commitment to quality and the environment, and a robust track record of reliability and customer satisfaction. By prioritizing these attributes, you ensure that your choice of manufacturer will meet specific needs with products that stand the test of time.