When it comes to construction materials, precision and quality are key. Welded wire mesh is vital to projects ranging from residential buildings to industrial complexes. A deep understanding of welded wire mesh gauge sizes is essential for ensuring the right fit for your project’s needs. This article delves into the intricacies of gauge sizes, offering insights drawn from industry expertise and practical experiences, emphasizing credibility and authority in the realm of construction materials.
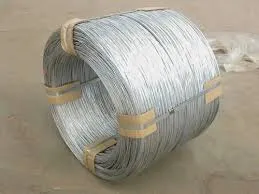
Welded wire mesh is composed of intersecting wires that are welded together at intersections to form a grid. The gauge of the wire refers to its thickness, which directly impacts the mesh’s strength, flexibility, and load-bearing capacity. Choosing the appropriate gauge is crucial for ensuring structural integrity and meeting project specifications.
The gauge size of welded wire mesh is typically measured using the American Wire Gauge (AWG) system or the Standard Wire Gauge (SWG) system, each with its own measurement criteria. As a general rule of thumb, the higher the gauge number, the thinner the wire. For instance,
a 16-gauge wire is thicker and stronger than a 20-gauge wire. This understanding is pivotal for those in the construction industry, where even minor discrepancies can lead to structural failures or increased costs.
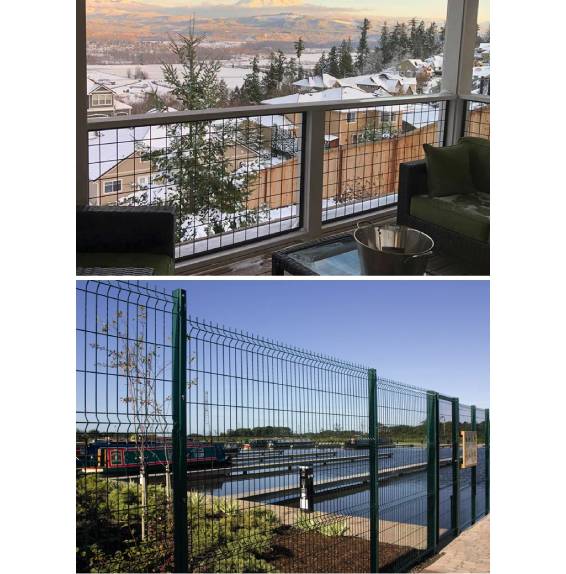
For residential applications, such as fencing or garden enclosures, lighter gauge meshes (typically ranging from 19-gauge to 23-gauge) are often sufficient. These provide adequate strength for light security needs while being more cost-effective. Expertise demands that one considers not only the security aspect but also aesthetics and ease of installation, where lighter gauges offer ease of maneuverability and installation without demanding specialized equipment.
In contrast, heavier gauge meshes (ranging from 10-gauge to 16-gauge) are indispensable in industrial settings. Such meshes are used in concrete reinforcement, heavy-duty fencing, and security barricades due to their superior strength and durability. Selecting the appropriate gauge size in these circumstances is not merely about supporting heavy loads but also about adhering to safety standards and regulations which dictate minimum requirements for wire mesh in specific applications.
welded wire mesh gauge sizes
Trustworthiness in choosing the right gauge size is enhanced by adhering to standards set by authoritative organizations such as the ASTM (American Society for Testing and Materials) or the ISO (International Organization for Standardization). These entities establish guidelines ensuring that materials meet necessary safety and quality benchmarks. Therefore, partnering with mesh suppliers who offer products conforming to these standards assures you of reliable and durable construction outcomes.
Practical experience often reveals the nuanced decisions involved in selecting the appropriate mesh gauge. For example, in regions prone to seismic activity, a finer gauge might suffice for flexibility and crack resistance in architectural finishes. However, heavier gauges are crucial for ensuring long-term durability under high stress. Consultation with seasoned engineers or professional builders can provide invaluable insights tailored to specific project contexts, reinforcing decisions with expert-backed credibility.
As projects evolve, future trends show an increasing demand for more sustainable and efficient building practices. In this context, knowledge of gauge sizes extends beyond conventional applications and into innovative solutions like modular walls or prefabricated structures. Here, the expertise lies in balancing traditional knowledge with cutting-edge techniques, ensuring that wire mesh not only supports existing structures but also contributes positively to the building’s lifecycle and environmental footprint.
In conclusion, a comprehensive understanding of welded wire mesh gauge sizes is indispensable for effective construction practices. Leveraging expertise in this area not only optimizes material use and cost but also ensures compliance with safety and quality standards. In an industry where precision is key, relying on authoritative and trustworthy sources, and engaging deeply with both theoretical knowledge and practical experience, is the blueprint for success.