Welded wire mesh rolls have become a cornerstone in numerous construction and industrial projects, thanks to their versatile applications and robust characteristics. For any construction professional or DIY enthusiast seeking grounded insights, this guide delves into the nitty-gritty of choosing and utilizing these indispensable materials.
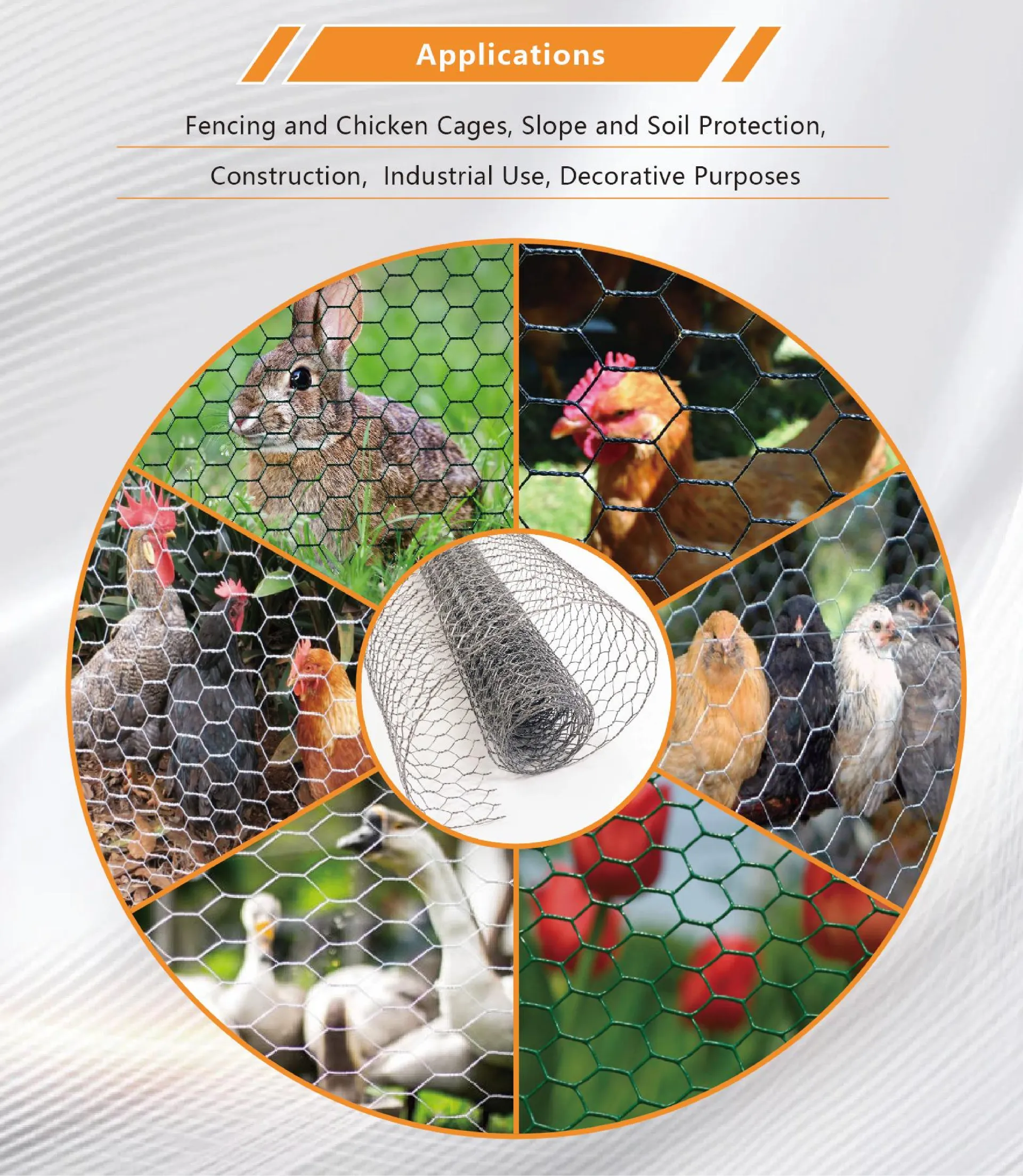
At its core, welded wire mesh rolls consist of intersecting wires that are welded together at each intersection, forming a grid-like pattern. This structure not only ensures strength but also provides a stable framework for concrete reinforcement, fencing, and other structural applications. The variety of materials, such as stainless steel, galvanized steel, and even PVC-coated versions, broadens their use across different environments, enhancing durability and resistance to corrosion.
Professionals in the field appreciate the strength-to-weight ratio of welded wire mesh. Unlike traditional rebar, which requires significant preparation and setup, wire mesh rolls are easy to handle and install. Their flexibility allows customization on site, making them ideal for projects that demand precision and adaptability. When considering ground reinforcement, for instance, the ease of rolling out the mesh and cutting it to size greatly reduces labor costs and time, yielding efficient project management.
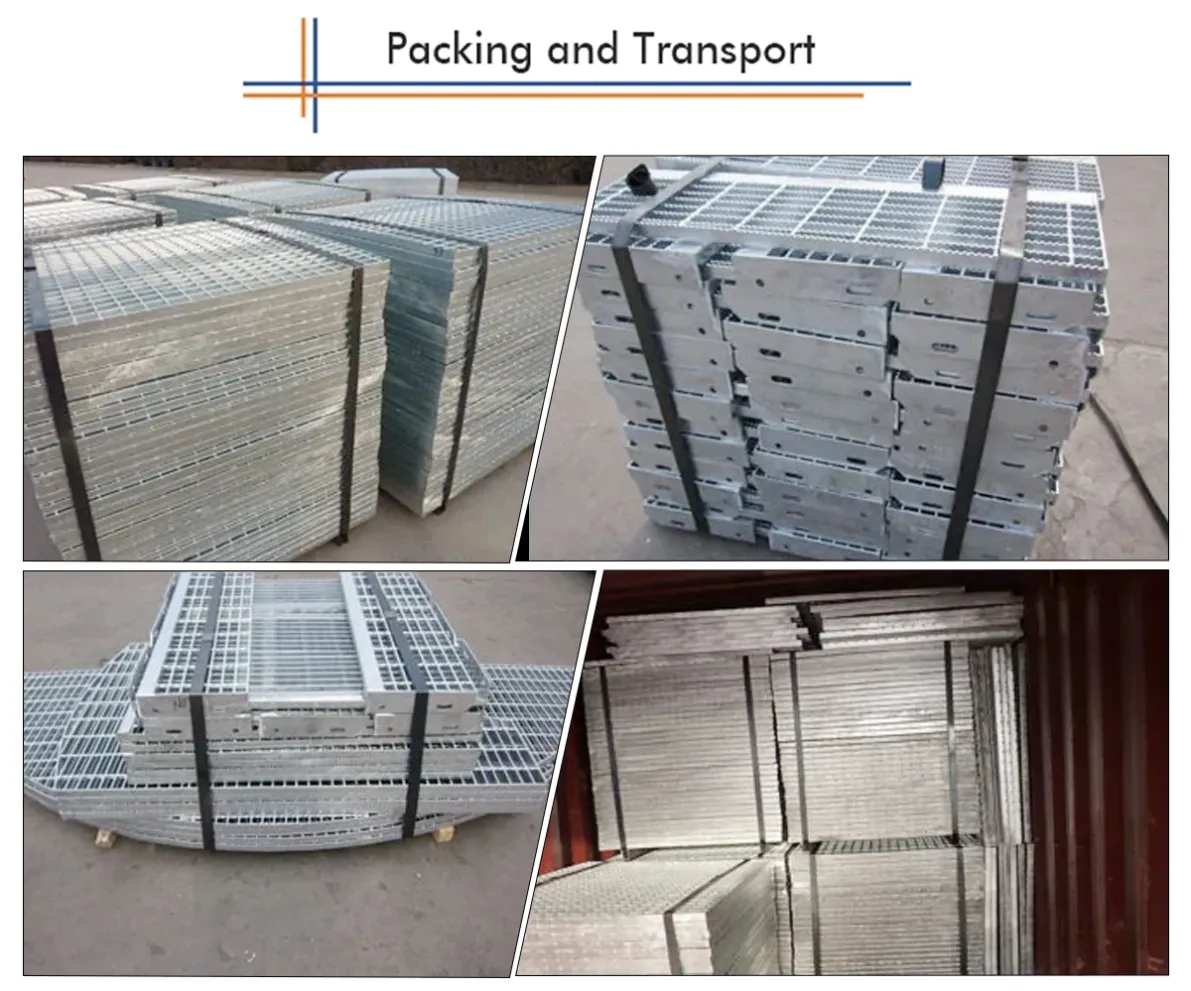
In terms of expertise, understanding the intricacies of wire gauge and opening size is crucial. Thicker wire gauges offer increased strength but may be less flexible, which can impact installation in confined or irregular spaces. Similarly, opening sizes determine the mesh’s suitability for certain tasks, with smaller openings offering better support for fine aggregate concretes. This knowledge empowers users to tailor their mesh selection for specific environmental and structural needs.
welded wire mesh rolls
Welded wire mesh rolls also shine in their authoritativeness within the industry. They adhere to stringent manufacturing standards, such as the ASTM (American Society for Testing and Materials) requirements, ensuring uniformity and quality control. This compliance guarantees that the mesh performs as expected when subjected to tensile stresses and environmental pressures, providing peace of mind to contractors and builders.
From a trustworthiness perspective, the long-term performance of welded wire mesh exceeds expectations. Numerous case studies affirm the mesh's ability to withstand harsh weather, heavy loads, and daily wear and tear over extended periods. Whether employed in highways, bridges, or residential buildings, the resilience and reliability of welded wire mesh rolls continue to reinforce their reputation as a go-to material.
For businesses and individuals investing in welded wire mesh rolls, the accumulation of these expert perspectives can influence smarter purchasing decisions and enhance project outcomes. When selecting a supplier, prioritize those with a proven track record, ensuring they offer mesh that meets both general and application-specific standards. The intersection of quality material, professional installation, and strategic application underscores the indispensable role of welded wire mesh in today's construction landscape.
In conclusion, welded wire mesh rolls are more than just a construction staple; they represent a blend of innovation, adaptability, and structural integrity. By understanding their attributes and effectively harnessing their capabilities, stakeholders across the construction spectrum can achieve efficiency, durability, and cost-effectiveness in their projects.