Welded wire mesh designation plays a critical role in various industries, offering a robust solution for both reinforcement and construction applications. Understanding the designation and its potential applications can greatly enhance your project outcomes.
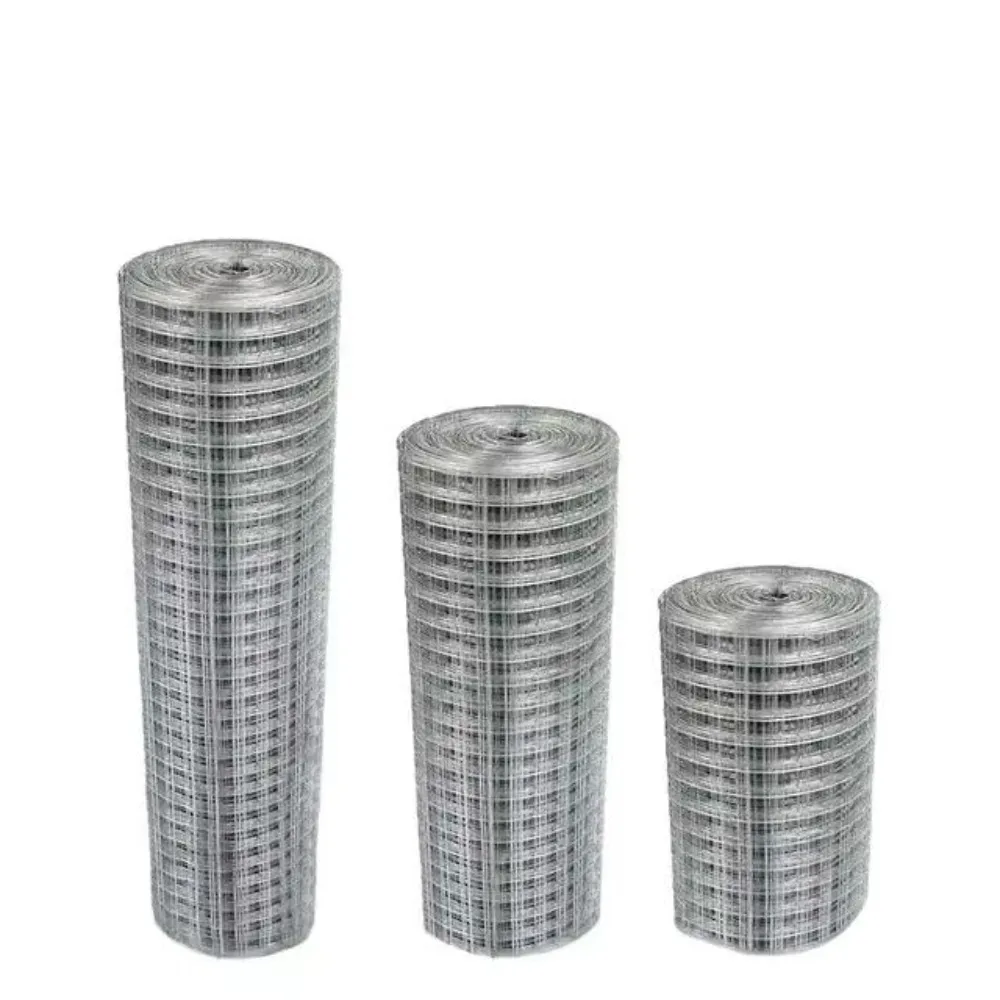
For decades,
welded wire mesh has served as a cornerstone in construction, agriculture, and industrial sectors. Constructed from intersecting wires electrically welded at all intersections, it forms a grid that offers exceptional strength and versatility. However, the effectiveness of this product hinges largely on understanding the specific designation that suits your requirements.
When selecting welded wire mesh, it's imperative to consider the gauge or diameter of the wire, the density of the mesh openings, and the overall dimensions of the sheet or roll. Each designation provides specific information that ensures the chosen mesh meets the technical requirements and structural demands of your project.
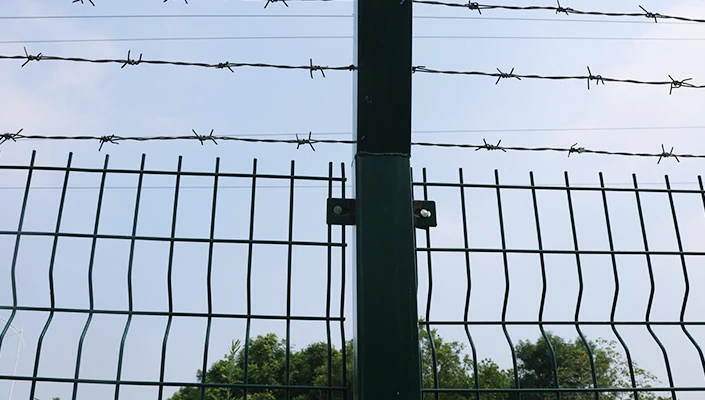
Gaining expertise in the designation of welded wire mesh requires familiarity with these key parameters
1. Wire Diameter The diameter of the wire used in the mesh determines the strength and flexibility of the final product. Ranging from light to heavy gauges, wire diameter influences the mesh's ability to bear weight, resist strain, and maintain structural integrity. For load-bearing applications, opting for a thicker gauge is advisable.
2. Mesh Size This refers to the dimensions of the space between the wires, impacting both the structural capacity and the intended application. Smaller mesh sizes enhance security and support, while larger ones may suit scenarios where weight reduction is critical. In construction, for example, tighter meshes are often preferred for their enhanced reinforcement capabilities.
welded wire mesh designation
3. Material Quality While steel is the most common material due to its strength and durability, variations such as galvanized or stainless steel offer enhanced resistance to corrosion, crucial for outdoor or exposed applications. Selection of material should align with environmental conditions to ensure longevity.
4. Sheet and Roll Dimensions Standard sheet sizes generally range between 1m x 1m to much larger dimensions, with the capability to produce custom sizes based on project needs. Roll dimensions can vary significantly and are typically determined by the length requirements for the job, offering flexibility in installation and reducing the need for joints or overlaps.
Another key factor in designation involves industry standards. Familiarity with ASTM, ISO, or other regional guidelines for welded wire mesh is imperative. These standards dictate permissible tolerances and performance benchmarks that can substantiate the mesh’s reliability and compliance with safety regulations.
On the practical side, real-world experience demonstrates the dual benefits of both cost-efficiency and time savings when using appropriately designated welded wire mesh. Installation is significantly expedited due to the prefabricated design, and its utilization often results in reduced labor costs. Moreover, the uniformity in wire spacing eliminates the guesswork associated with manual rebar tying, leading to more consistent results.
Trustworthiness of the welded wire mesh you select is inextricably linked to the credibility and reputation of the manufacturer. Choosing well-established manufacturers with a proven track record ensures product quality and adherence to industry standards, fostering confidence in performance and outcome.
In summary, expertise in welded wire mesh designation is essential for optimizing its application to your specific needs. By paying close attention to wire diameter, mesh size, material composition, and dimensions, and aligning them with industry standards, you can achieve superior results. Furthermore, leveraging products from reputable manufacturers enhances not only the efficacy of your project but also reinforces the trust and reliability necessary for successful execution. With the right knowledge, welded wire mesh becomes an indispensable asset in building safer, more efficient, and durable structures.