In the realm of construction and infrastructure projects, the selection of materials can significantly influence the longevity and resilience of the structures being built.
Among these essential materials is the welded wire fabric, a vital component in concrete reinforcement. Selecting the appropriate welded wire fabric sizes is crucial for both the integrity and success of any construction project.
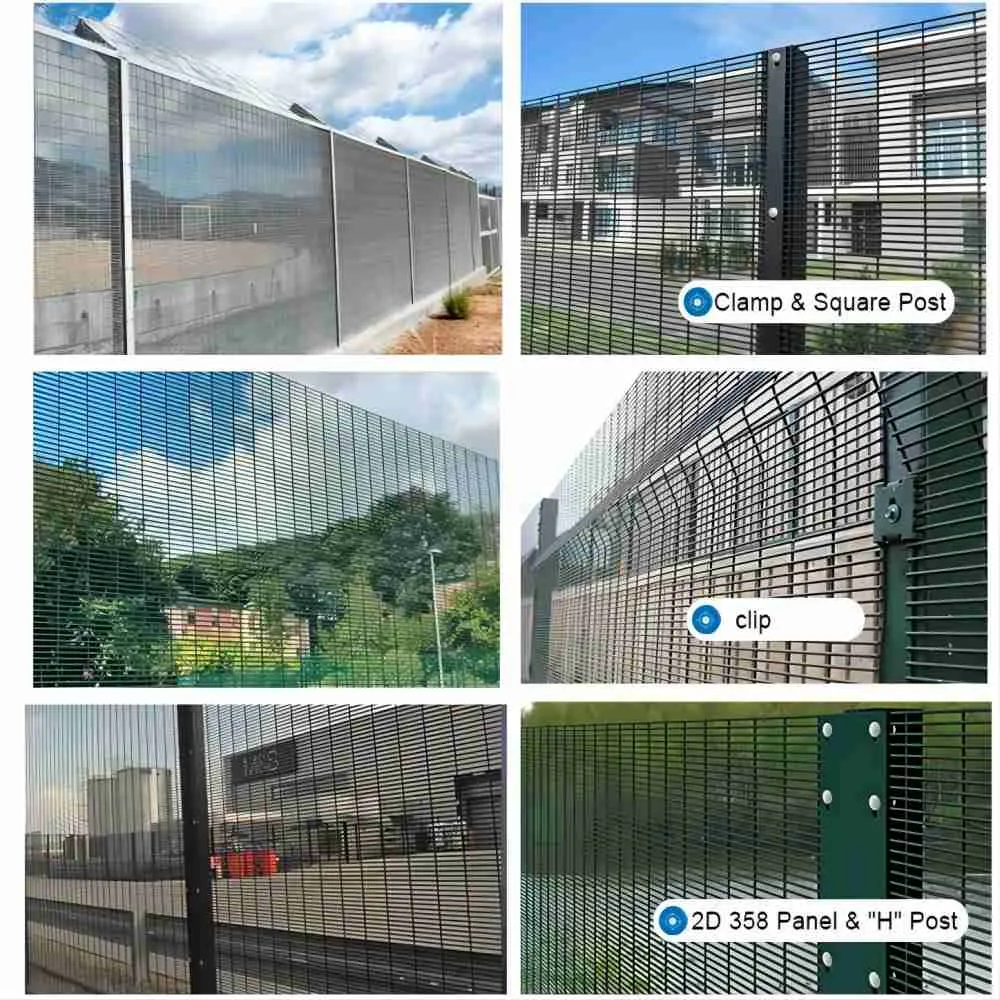
Understanding the Role and Importance of Welded Wire Fabric
Welded wire fabric, often abbreviated as WWF, consists of intersecting steel wires welded into a grid configuration. Its primary purpose is to reinforce concrete and other construction materials, enhancing tensile strength and ensuring structural stability. The grids are created with wires of varying thickness, and the intersections are welded, ensuring a robust bond that can withstand substantial pressure and force.
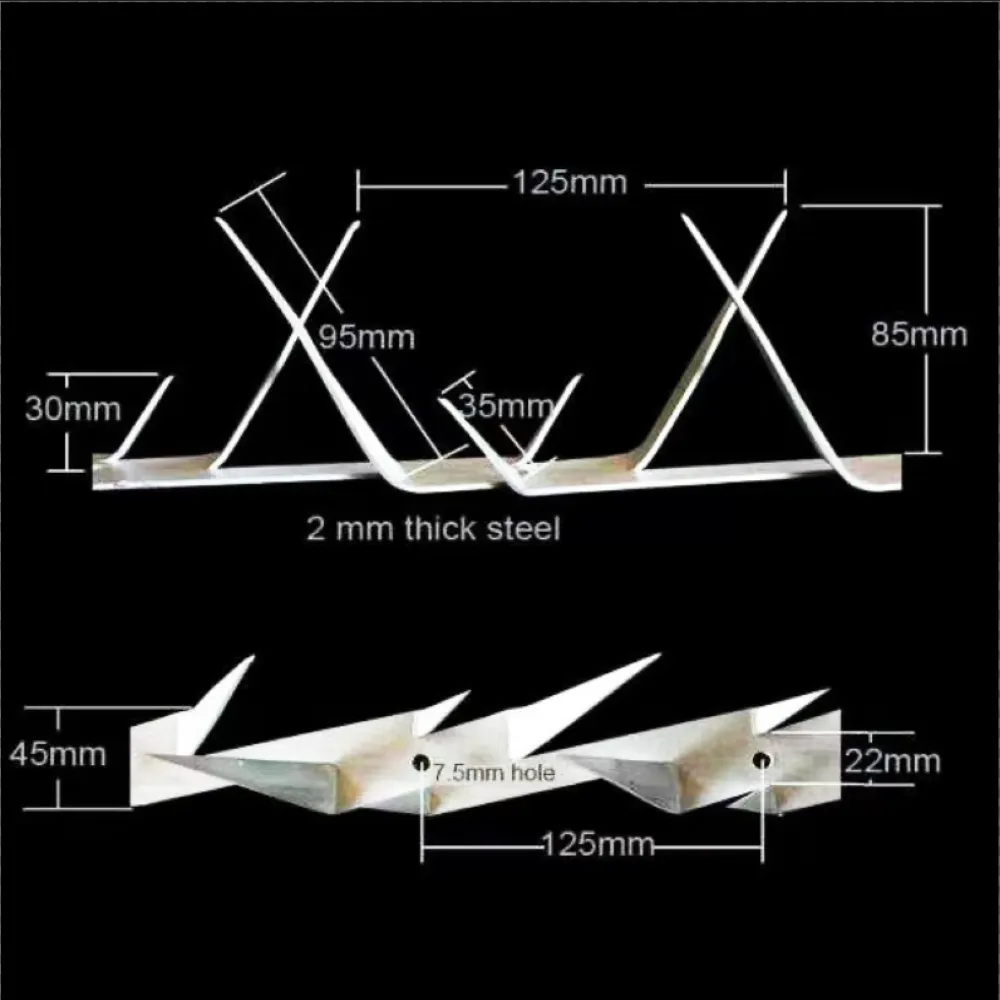
Reinforcing concrete with WWF is akin to fortifying the skeleton of a building. While concrete is excellent under compression, it is comparatively weak under tension. By integrating welded wire fabric into the concrete, it compensates for this weakness, making the material far more resilient.
Choosing the Right Sizes Key Considerations
The dimensions of welded wire fabric, including the gauge of wire and the spacing of the grids, are critical in its application. The choice largely depends on the requirements of the construction project, taking into account the loads and stresses the concrete will encounter.
1. Gauge of Wire The thickness of the wire, represented in gauges, is one critical factor. Thicker wires generally offer stronger reinforcement but may also demand more concrete coverage. For large-scale projects such as bridges and high-rise buildings, a thicker gauge is advisable, while smaller projects, like sidewalks or driveways, might suffice with a lighter gauge.
2. Grid Spacing Spacing refers to the distance between each wire in the grid. Typically measured in inches, grid spacing determines how force is distributed across the concrete slab. Closer grid spacing provides more reinforcement, which is beneficial for high traffic areas and industrial floors that endure extensive wear and tear.
3. Roll Length and Width These dimensions determine the coverage of the fabric. Longer and wider rolls reduce the number of seams, which can serve as weak points in the concrete. For seamless applications with minimal potential failure points, choosing appropriate width and length is fundamental.
Application-Specific Selection
Different construction applications dictate specific size selections for welded wire fabric
welded wire fabric sizes
- Driveways and Parking Lots These typically require a medium gauge wire with a moderate grid spacing to withstand vehicle weight and environmental wear.
- Foundations and Basement Walls Heavier gauge wire with tighter grid spacing is ideal, as it provides the necessary tensile strength to support vertical loads and resist lateral earth pressures.
- Infrastructure Projects (Bridges, Overpasses) These necessitate the highest level of reinforcement. Thus, a thick gauge with minimal grid spacing is chosen to resist both dynamic loads and static pressures.
The Authority of Standards and Specifications
Adherence to industry standards and specifications is paramount in choosing the right welded wire fabric size. Institutions like the American Society for Testing and Materials (ASTM) provide comprehensive guidelines to ensure that materials meet the requisite performance criteria. These standards cover aspects such as material properties, testing methods, and dimensions, imparting confidence in the structural integrity and safety of the construction.
Moreover, consulting with structural engineers and material experts can offer bespoke solutions tailored to the unique demands of any given project. Their expertise ensures compliance with local building codes and maximizes the material's effectiveness, further guaranteeing a successful and durable outcome.
The Trust Factor Reliability and Quality Assurance
Selecting high-quality welded wire fabric from reputable manufacturers is non-negotiable. Inferior products risk the safety of the entire structure, leading to potential failures and costly reconstructions. Thus, manufacturers should have transparent quality control measures and provide certifications that validate the strength, durability, and reliability of their products.
Expert Insights and Real-World Experiences
Professionals in the field often emphasize the importance of real-world testing and simulations. Experienced engineers and contractors sometimes engage in pilot studies or experimental projects to evaluate the performance of different welded wire fabric sizes in situ. These insights are invaluable, providing data that informs future decision-making and reinforces the empirical knowledge base.
In conclussion, understanding and selecting the correct welded wire fabric sizes are essential for any successful construction endeavor. By considering wire gauge, grid spacing, and adherence to industry standards, project leaders can ensure the structural fidelity and longevity of their builds, ultimately contributing to a resilient and dependable infrastructure.