Understanding the weight characteristics of welded wire mesh products is crucial for those in construction, agriculture, or industrial sectors. The welded wire mesh is not only important because it serves structural purposes, but also because its weight directly influences both shipping costs and structural integrity.
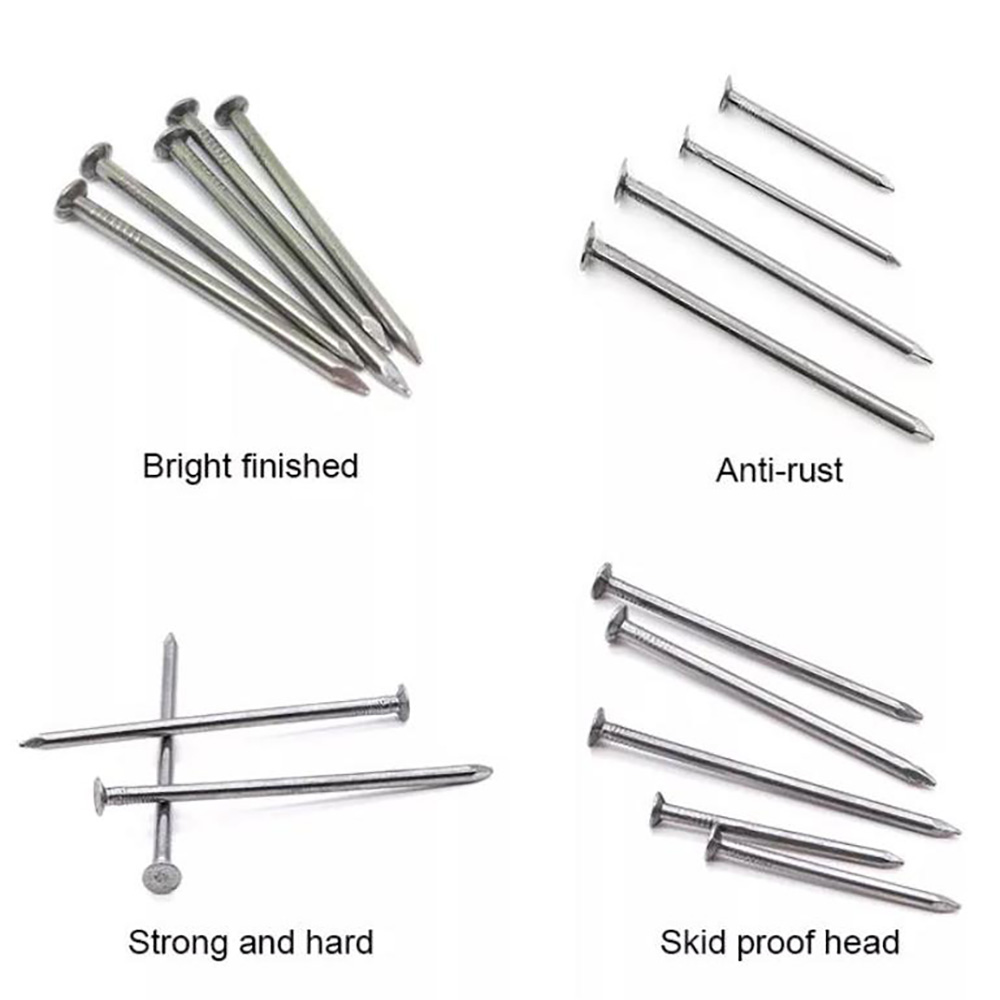
To start, what exactly is welded wire mesh? It is a grid of wires that are welded at their junctions at right angles to each other. The material can be made from a variety of metals with varying thicknesses, and it is commonly used in construction for reinforcing concrete, fencing, and in various design applications as well.
Welded wire mesh is available in different gauges and openings and is used in diverse applications such as perimeter fencing, garden fencing, concrete reinforcement, and even in artistic projects or complex architectural designs. The weight of the mesh is a significant parameter for determining its suitability for specific applications.
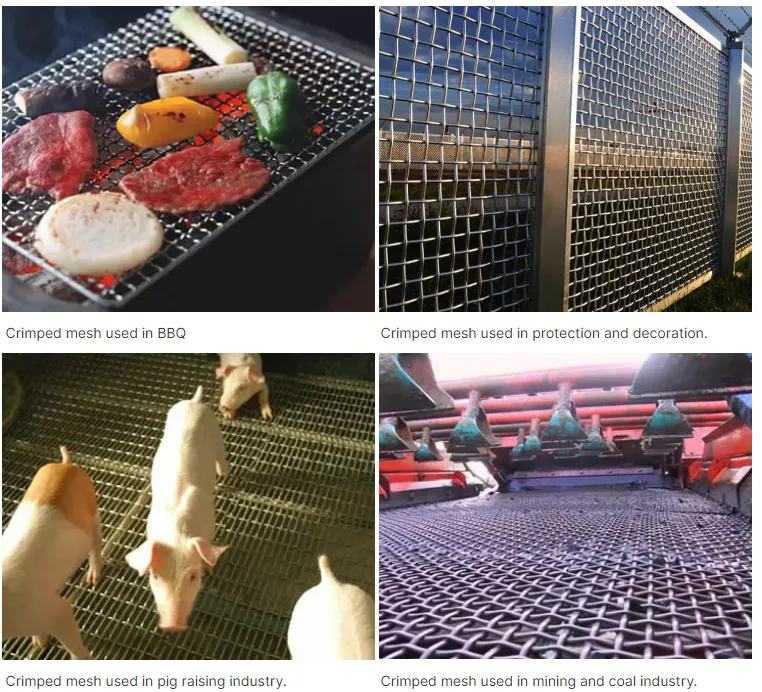
Calculating the weight of welded wire mesh involves several factors, including wire diameter, aperture size, wire spacing, and sheet dimensions. Generally, as wire diameter and mesh density increase, so does the weight. For instance, a mesh with closely packed wires woven in a pattern will weigh more than a similar mesh with wider apertures.
Why does this matter? First, the weight has implications for transporting and handling the mesh. Heavier mesh costs more to move, and laborers will require more effort to maneuver it during installation, potentially impacting project timelines and costs.
Moreover, weight plays an essential role in the performance of the welded wire mesh when used in reinforcement applications. Heavier wire meshes provide greater tensile strength and support and are thus more appropriate for projects where high load-bearing capacity is required. On the other hand, for decorative or less-intensive reinforcement tasks, a lighter mesh might be more cost-effective and simpler to install.
welded wire mesh weight chart
Accuracy in determining the weight is paramount, especially in bulk purchases. Therefore, businesses need reliable weight charts that clearly show the weight per square foot for various wire diameters and mesh sizes. This helps in making informed decisions quickly, thereby enhancing efficiency.
Furthermore,
the manufacturing process of welded wire mesh also affects its weight. Galvanization, a standard procedure for preventing rust, adds a small weight to the overall product but significantly increases its lifespan and durability, which is beneficial in outdoor or moisture-prone environments.
Experts within the industry emphasize the importance of referencing a comprehensive welded wire mesh weight chart to ensure you select the most suitable product for your specific application. Such charts provide valuable insight into which mesh type provides the best balance of weight and durability, thus optimizing your structural or operational design.
Ensuring the credibility and reliability of the source of weight charts is crucial. Trustworthy manufacturers and suppliers should provide verified data, sometimes derived from standardized tests and quality certifications, ensuring the products meet industry benchmarks for safety and performance.
Finally, employing specialists who understand welded wire meshes' technical specifications can further assure project success. Their expertise can aid in selecting the right type of mesh, accurately interpreting weight charts, and recognizing how these choices will impact the overall project.
Consequently, selecting the correct welded wire mesh involves comprehending its weight characteristics through detailed charts, understanding the implications of wire diameters and aperture sizes, and recognizing the added value of proper treatments like galvanization. This tailored approach ultimately leads to better purchasing decisions, optimized project execution, and increased longevity of the wire mesh solutions you implement.