The Evolution of Binding Wire Gauge for Enhanced Electrical Connections
In the realm of electrical engineering, the importance of wire gauge cannot be overstated. It serves as the backbone of our intricate electrical systems, determining the current-carrying capacity and overall efficiency of the connections it facilitates. As technology advances, so too does the need for more precise and reliable wiring methods. This has led to a significant evolution in binding wire gauge standards, ensuring that we can meet the ever-growing demands of modern electrical systems.
The journey of binding wire gauge began with the earliest electrical installations, where wires were typically large and bulky due to limitations in materials and manufacturing processes. However, as the demand for smaller, more compact devices grew, so did the need for thinner wires that could accommodate higher current loads without compromising on performance.
This led to the development of standardized wire gauges, with each gauge representing a specific diameter. The most commonly used system is the American Wire Gauge (AWG), which ranges from 0000 (the thinnest) to 40 (the thickest). Each gauge increase represents a decrease in wire diameter and an increase in current-carrying capacity.
One of the key factors driving the evolution of binding wire gauge is the increasing use of electronic devices and systems that require high levels of precision and reliability
One of the key factors driving the evolution of binding wire gauge is the increasing use of electronic devices and systems that require high levels of precision and reliability
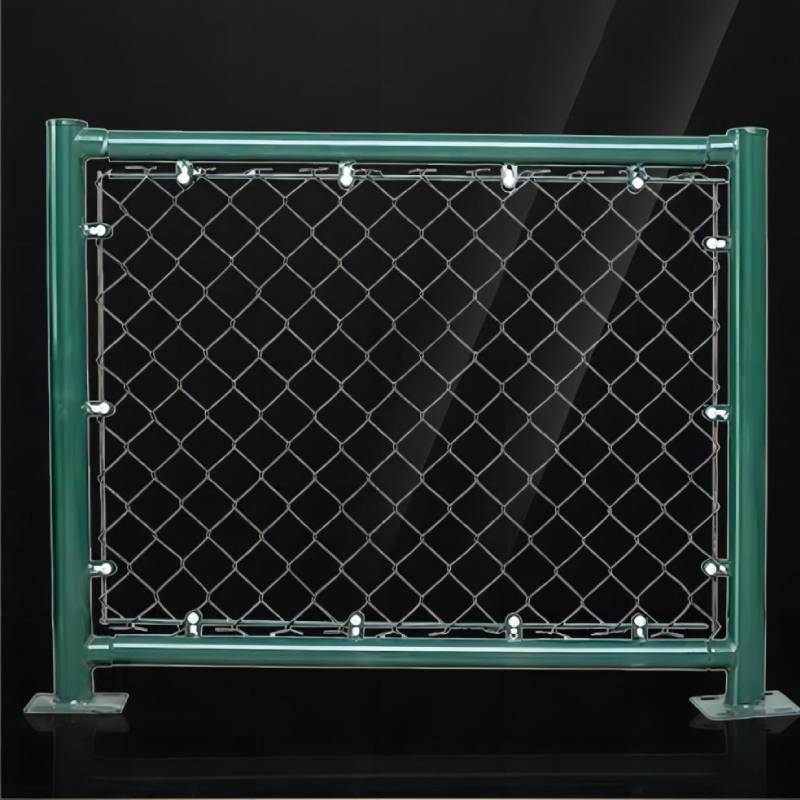
One of the key factors driving the evolution of binding wire gauge is the increasing use of electronic devices and systems that require high levels of precision and reliability
One of the key factors driving the evolution of binding wire gauge is the increasing use of electronic devices and systems that require high levels of precision and reliability
binding wire 21 gauge. For example, in the automotive industry, the use of advanced electrical systems has increased significantly in recent years, necessitating the use of thinner wires with higher conductivity to reduce weight and improve fuel efficiency. Similarly, in the aerospace industry, where space and weight are at a premium, the use of binding wire with precise gauge control is crucial for ensuring the safe and reliable operation of critical systems.
In addition to improved performance, the evolution of binding wire gauge has also led to significant cost savings. Thinner wires are generally less expensive to produce than thicker ones, making them a more cost-effective option for many applications. Furthermore, the ability to use a wider range of wire gauges allows engineers to optimize their designs for specific requirements, further reducing costs and improving overall system efficiency.
In conclusion, the evolution of binding wire gauge is a testament to the ingenuity and innovation of the electrical engineering community. By continuously refining and improving our understanding of wire properties and performance, we have been able to develop a wide range of wire gauges that meet the diverse needs of modern electrical systems. As technology continues to advance, we can expect to see further refinements and developments in this field, enabling us to create even more efficient and reliable electrical connections.