Iron winding wire is a critical component in various industrial and consumer applications, ranging from transformers to electric motors. Understanding its profound impact on performance and reliability requires a deep dive into its properties, applications, and the expertise needed for its optimal use.
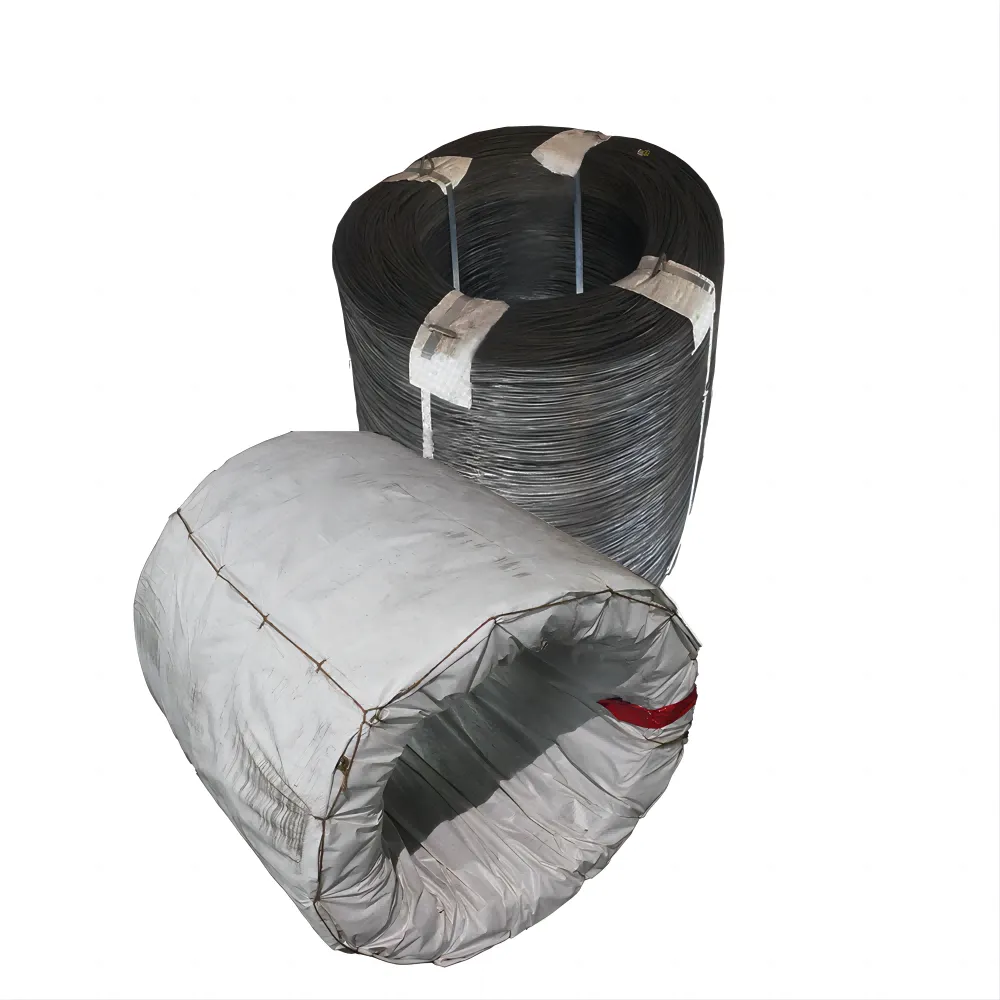
Iron winding wire stands out due to its ferromagnetic properties, which significantly enhance the efficiency of energy transfer in electromagnetic applications. The wire is engineered to withstand high temperatures, often reaching up to 200°C, making it suitable for demanding environments. This heat resistance is crucial in preventing insulation breakdown, ensuring longevity and reliable performance in continuous duty applications.
In the realm of expertise, producing high-quality iron winding wire involves a meticulous manufacturing process. The wire must be drawn and annealed carefully to ensure optimal conductivity and mechanical stability. Its insulation is typically made from polyimide or other high-temperature polymers, applied through precision extrusion or enameling techniques. This insulation not only provides electrical isolation but also contributes to the wire's durability by protecting it from environmental factors and mechanical wear.
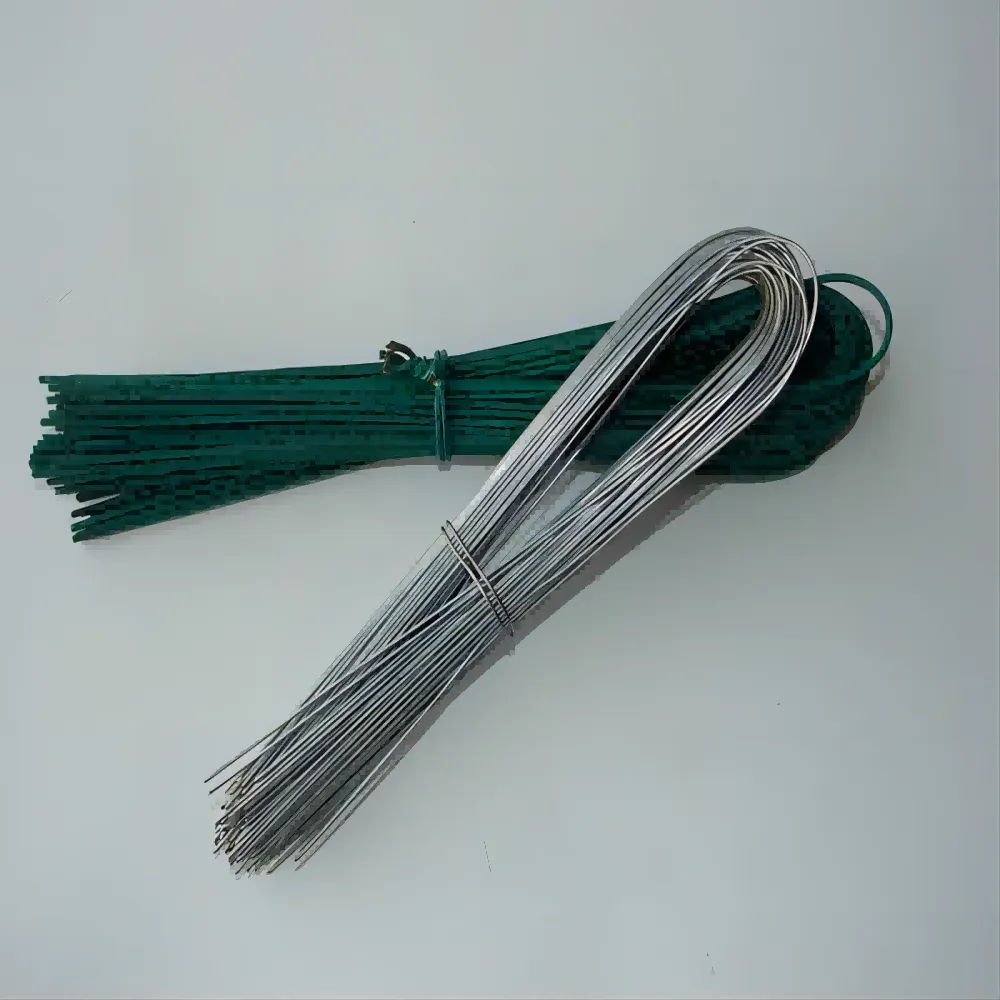
Professionals who utilize iron winding wire in their products, like electric motor manufacturers, rely heavily on its performance specifications. These include tensile strength, elongation, and moisture resistance, all of which contribute to the wire's ability to maintain magnetic properties over extended cycles of use. Engineers designing motors employ specific winding techniques that maximize the magnetic field generated while minimizing loss. This requires an authoritative understanding of the wire's electrical characteristics and its interaction with other motor components.
iron winding wire
For those in the transformer industry, trust in iron winding wire is rooted in its contribution to energy efficiency and regulation. The wire must be precisely layered to form windings that uniformly distribute electrical load, reducing loss and preventing overheating. Knowledge of electromagnetic theory and thermal dynamics is essential for engineers tasked with these designs, ensuring that transformers not only meet current standards but also future-proof against higher demand cycles.
From a consumer perspective, products incorporating iron winding wire are often judged by their longevity and energy efficiency. Consumers invest in goods like electric vehicles or home generators, knowing that the quality and reliability of the winding wire play a pivotal role in overall product performance. Trust is further established through certifications and compliance with international standards, such as UL and IEC, which these wires typically carry. Research and development teams continually test and refine wire formulations to surpass these standards, incorporating feedback from real-world application to enhance product offerings.
In conclusion, the significance of iron winding wire extends far beyond its physical properties. It embodies a synthesis of specialized expertise, rigorous manufacturing processes, and stringent quality controls, ensuring that it remains an authoritative choice in countless applications. Its role in shaping energy-efficient technologies and durable products underscores the need for continued innovation and trustworthiness in its production and use, setting a benchmark for quality and reliability in an ever-evolving industrial landscape.