In the world of construction and industrial applications, welded wire mesh has emerged as an essential component, offering versatility, strength, and ease of use. Understanding the manufacturing process of welded wire mesh is crucial for anyone involved in related industries, whether they are builders, engineers, or suppliers. This process guarantees that the final product meets the required standards of durability and functionality, embodying expertise, authority, and trustworthiness.
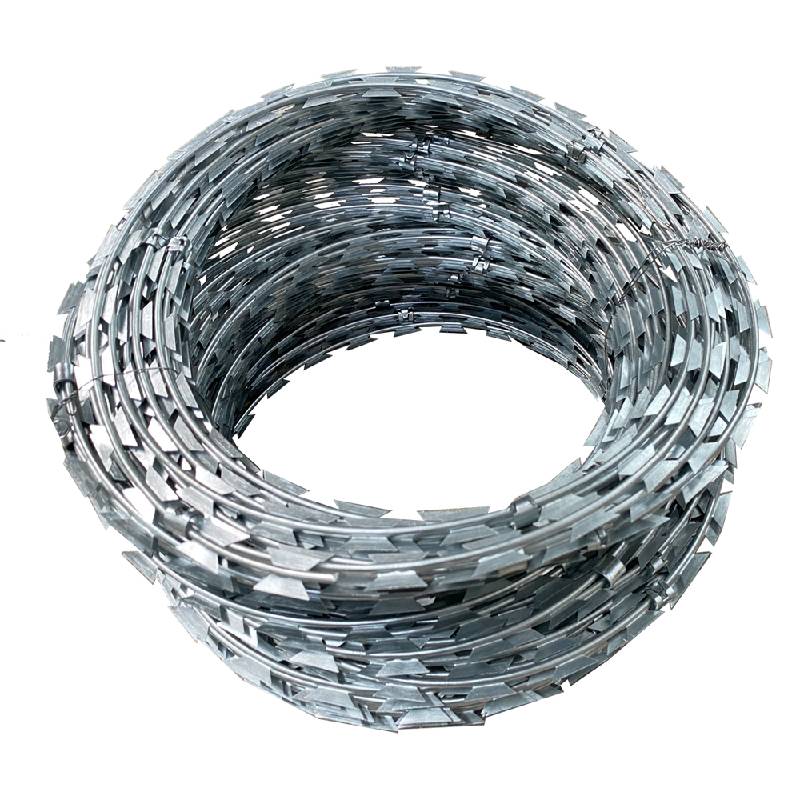
Starting with the raw materials, manufacturing welded wire mesh begins with selecting high-quality steel wires. These wires are typically made from mild steel, galvanized steel, or stainless steel, depending on the desired properties of the final mesh. The choice of material directly affects the mesh's durability, corrosion resistance, and flexibility. Ensuring the use of top-grade materials is the first step to gaining trust in product quality and longevity.
Once the wires have been selected, the next step involves straightening and cutting them to the required length. This process is carried out using precision machinery that guarantees accuracy and consistency. Expertise in handling these machines is paramount as it dictates the structural integrity of the mesh. Accurate cutting ensures that the pieces fit perfectly during the welding process, minimizing waste and maximizing efficiency.
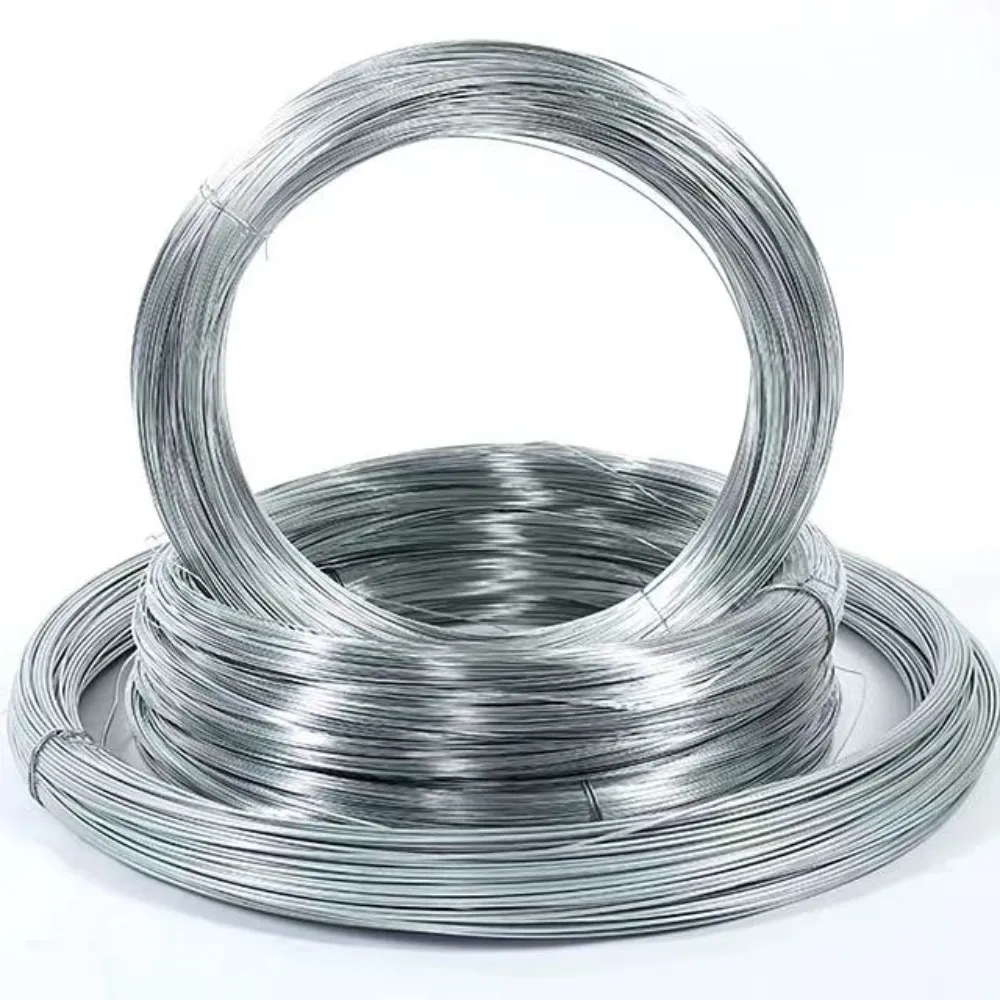
The core of the manufacturing process is the welding stage. Here, longitudinal and transverse wires are fused at their intersections using welding machines. The automated process uses electrical resistance to generate enough heat to melt and fuse the wires together. Depending on the application, various welding patterns such as square, rectangular, or customized grids can be produced. These patterns influence the tensile strength and load-bearing capacity of the welded mesh, underlining the importance of expertise in selecting the appropriate configuration for specific applications.
welded wire mesh manufacturing process
Quality control is an essential element that intersperses throughout the manufacturing process. At each stage, from material selection to cutting and welding, rigorous checks are in place to ensure that every piece of the wire mesh meets industry standards and customer specifications. For instance, tests for tensile strength, weld shear strength, and corrosion resistance are conducted to verify the mesh’s capability to withstand various conditions. This systematic approach to quality assurance fosters authority and trustworthiness, reassuring clients of reliable and robust products.
After the mesh is welded and quality-checked, it undergoes surface treatment. This step is crucial in enhancing the mesh's resistance to environmental factors. For instance, galvanization may be performed to protect against rust and corrosion, making the mesh suitable for outdoor and demanding environments. Alternatively, other coatings like PVC or powder coating can be applied to improve durability and aesthetic appearance. By offering these additional options, manufacturers enhance their reputability and authority, demonstrating a commitment to customer satisfaction and diverse application needs.
The final phase in the manufacturing process is packaging and distribution. The mesh is cut into panes or rolled according to the user’s needs, ensuring convenient handling and transportation. Efficient and safe packaging is essential to maintain the mesh’s condition during shipment. This is where trust is cemented; receiving the product in pristine condition assures clients of the manufacturer's reliability.
In conclusion, welded wire mesh manufacturing is a meticulous process that requires in-depth expertise and unwavering commitment to quality at every stage. From raw materials selection, precision cutting, innovative welding techniques, rigorous quality control, to effective surface treatments and packaging, each step is designed to optimize the product’s performance and reliability. The seamless integration of these procedures establishes authority and builds trust with clients, guaranteeing a product that meets and exceeds industry standards.