Welded wire mesh, a popular construction and material choice in modern architecture and industry, plays a significant role in reinforcing structures and providing support solutions across various applications. Understanding the nomenclature is crucial for architects, engineers, and construction professionals to make informed decisions regarding its usage.
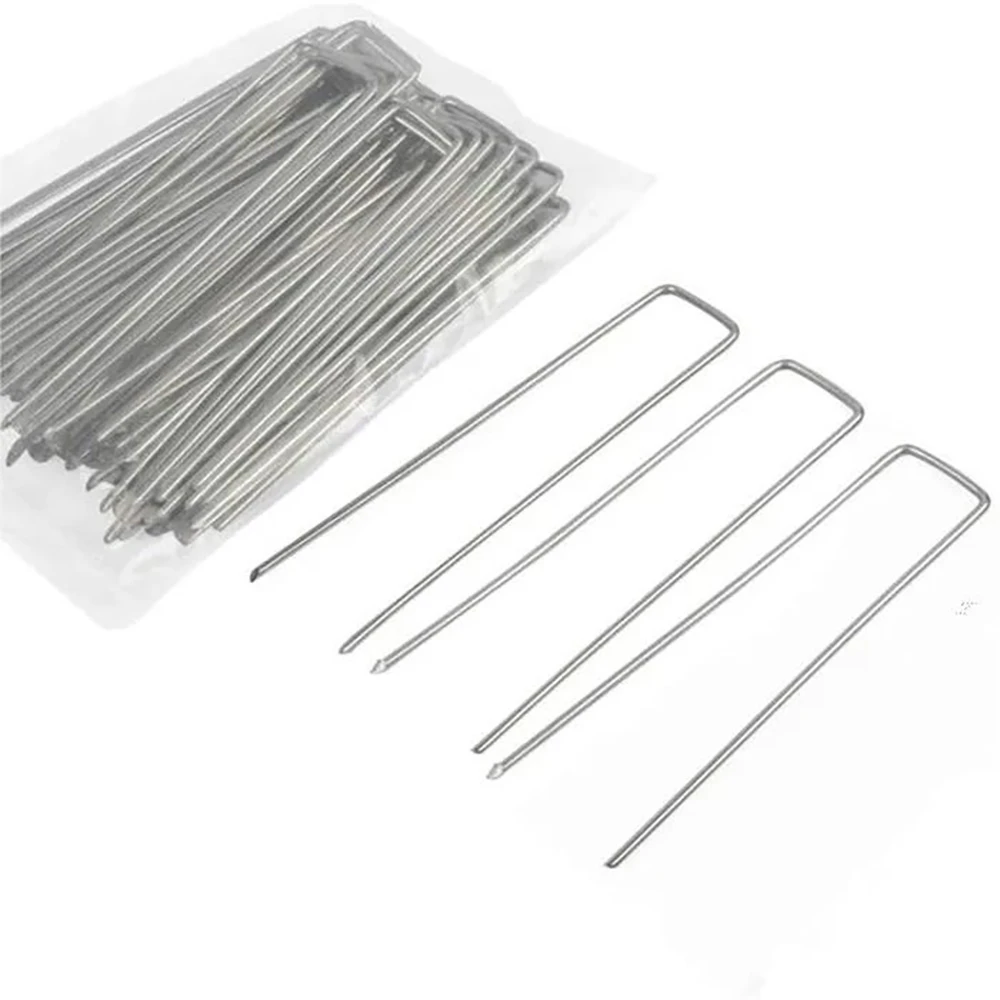
To begin with, welded wire mesh is manufactured by electrically welding wires at all intersections, providing enhanced strength and durability. It is commonly available in rolls or flat panels, and the grid pattern can be square or rectangular, depending on specific project requirements. Identifying these specifications is the first step for anyone venturing into projects requiring durable structural reinforcements or material support.
The nomenclature of welded wire mesh is a systematic way of conveying important specifications about the product. This method typically includes information about the diameter of the wire, the spacing between the wires, and the dimensions of the mesh. Knowing how to accurately decipher this code ensures that the right type of mesh is selected for the job, which is crucial for maintaining structural integrity and safety. Imagine a scenario where a construction professional selects the wrong mesh due to a misunderstanding of the nomenclature; the repercussions could be not just costly but also potentially dangerous.
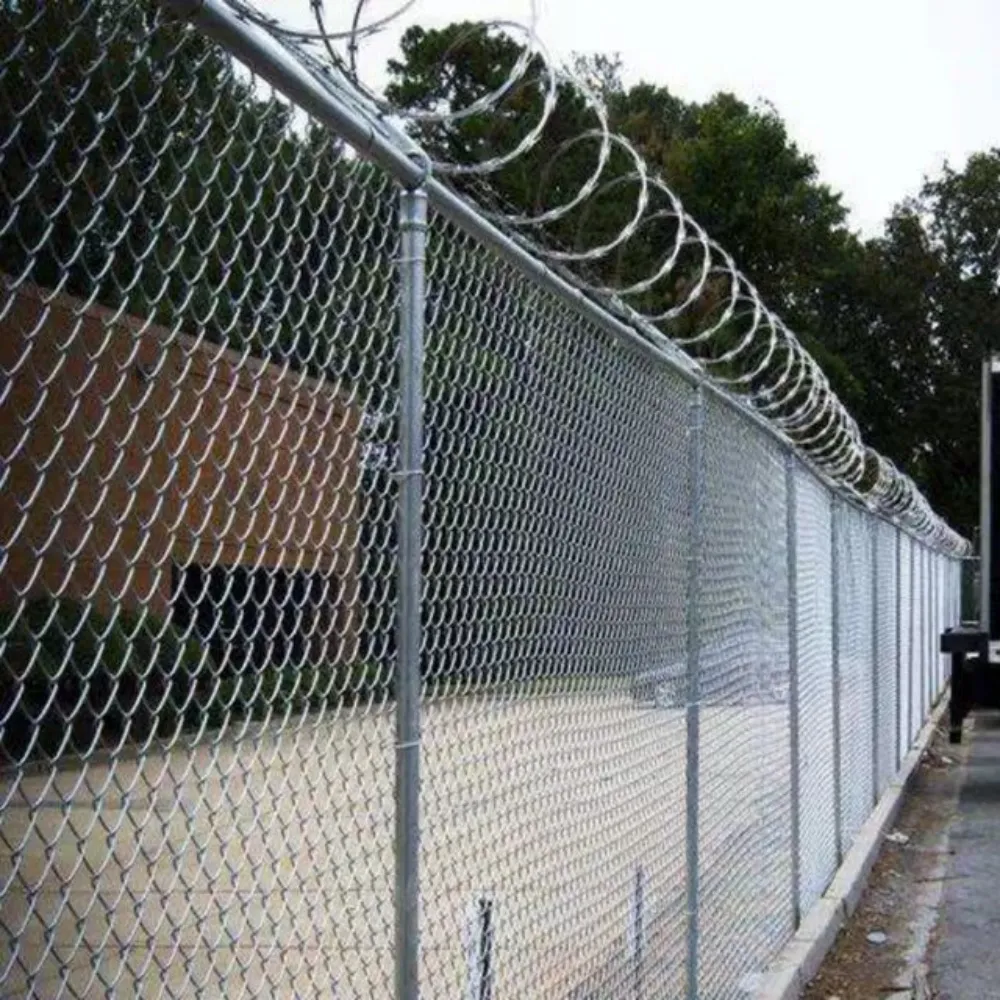
Among the common types of welded wire mesh, ‘plain welded wire mesh’ uses mild steel wires, while a galvanized version of this mesh offers enhanced corrosion resistance, making it ideal for outdoor applications. The decision between plain or galvanized often hinges on environmental conditions and lifespan expectations. Our expertise in this area reveals that a well-chosen galvanized mesh can significantly extend the service life of a structure, particularly in regions with high rainfall or saline exposure.
welded wire mesh nomenclature
Welded wire mesh is often specified using a series of numbers and letters that might seem confusing at first. For instance, an identifier like WWF 8x8-W1.4/W1.4 can seem perplexing but is informative once understood. The first sequence, ‘8x8’, indicates the spacing of the wires in inches, while the ‘W1.4’ denotes the wire gauge or diameter in terms of cross-sectional area. Mastery of this nomenclature ensures not only the acquisition of appropriate materials but also the seamless integration of them into the design process, enhancing the overall quality of the construction.
Beyond construction, welded wire mesh is utilized in industrial applications, such as cages, racks, and even artistic installations. Each of these uses benefits immensely from the bespoke capabilities offered by understanding and utilizing the correct mesh specifications. In our years of experience dealing with industrial applications, optimized mesh solutions have frequently translated to increased efficiency and reduced material wastage, directly impacting the bottom line positively.
Trust in a welded wire mesh provider is built through transparency and quality assurance. We recommend partnering with manufacturers who adhere to industry standards, such as the ASTM or ISO specifications, to ensure product quality and consistency. These manufacturers provide test certificates and specifications, offering credible solutions which boost trust for professionals relying on their products.
In conclusion, the nomenclature of welded wire mesh is more than just an identifier for a product; it is a key part of project planning and execution. Knowledge of this nomenclature empowers professionals to make informed choices, ensuring safety, efficiency, and durability in construction and industrial applications. Investing time in understanding the intricacies of wire mesh selections not only saves time and resources but significantly enhances project outcomes. With our industry insights and expertise, we advocate for a knowledgeable approach to selecting welded wire mesh, fortified by trust and credibility in the sourcing processes.