Welded wire mesh has become an integral component in modern construction and industrial projects due to its versatility and strong structural properties. To leverage its full potential, it’s crucial to understand the specifications and technical nuances that make this product highly effective and widely applicable.
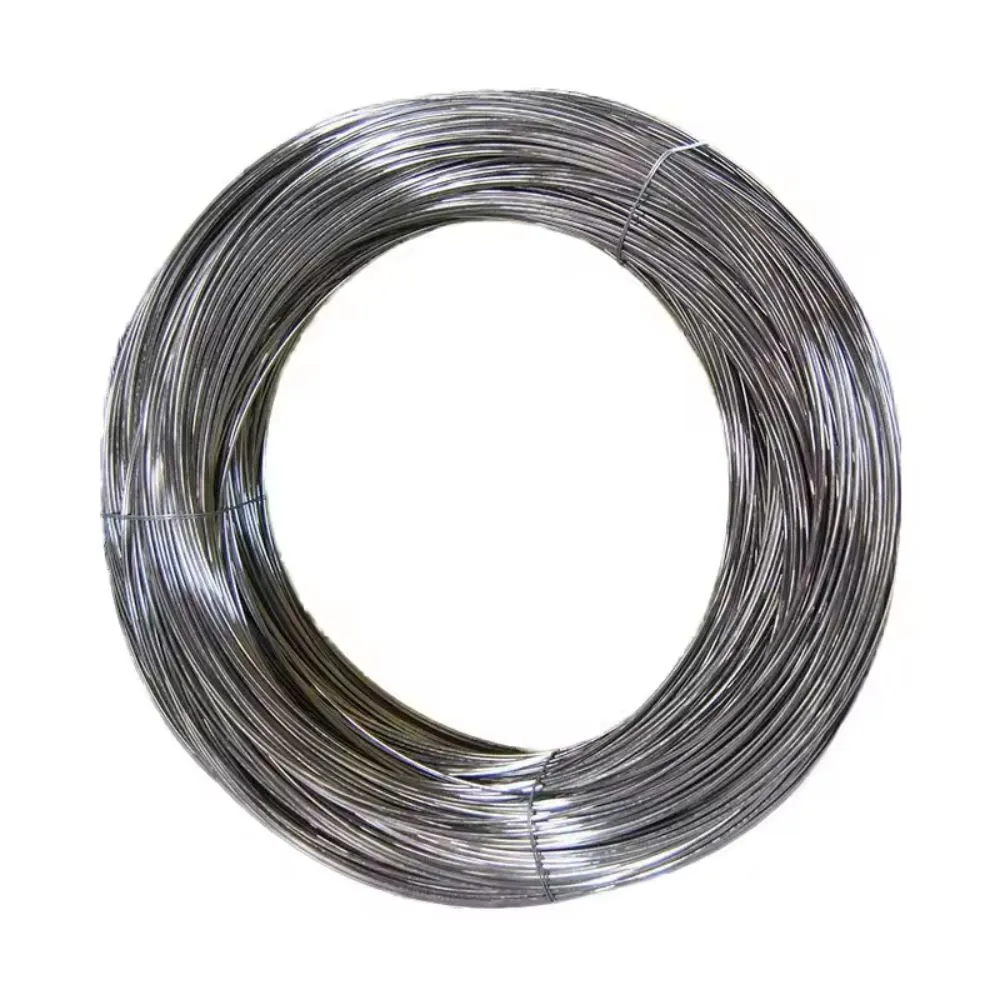
Welded wire mesh is a series of parallel longitudinal wires welded together with accurate spacing using cross wires. This configuration offers a grid-like structure that's pivotal for reinforcing concrete, fencing, and various other applications. The welds provide the mesh with substantial strength and rigidity, ensuring it can withstand substantial stress and load.
One primary consideration in selecting welded wire mesh is the gauge of the wire used. This gauge determines the thickness and strength of the mesh. For construction applications, a thicker gauge is typically utilized, providing increased tensile strength and durability. Common gauges range from 10 to 16, where a lower number indicates a thicker, stronger wire. Understanding the gauge is vital, especially for projects requiring enhanced support and load-bearing capacities.
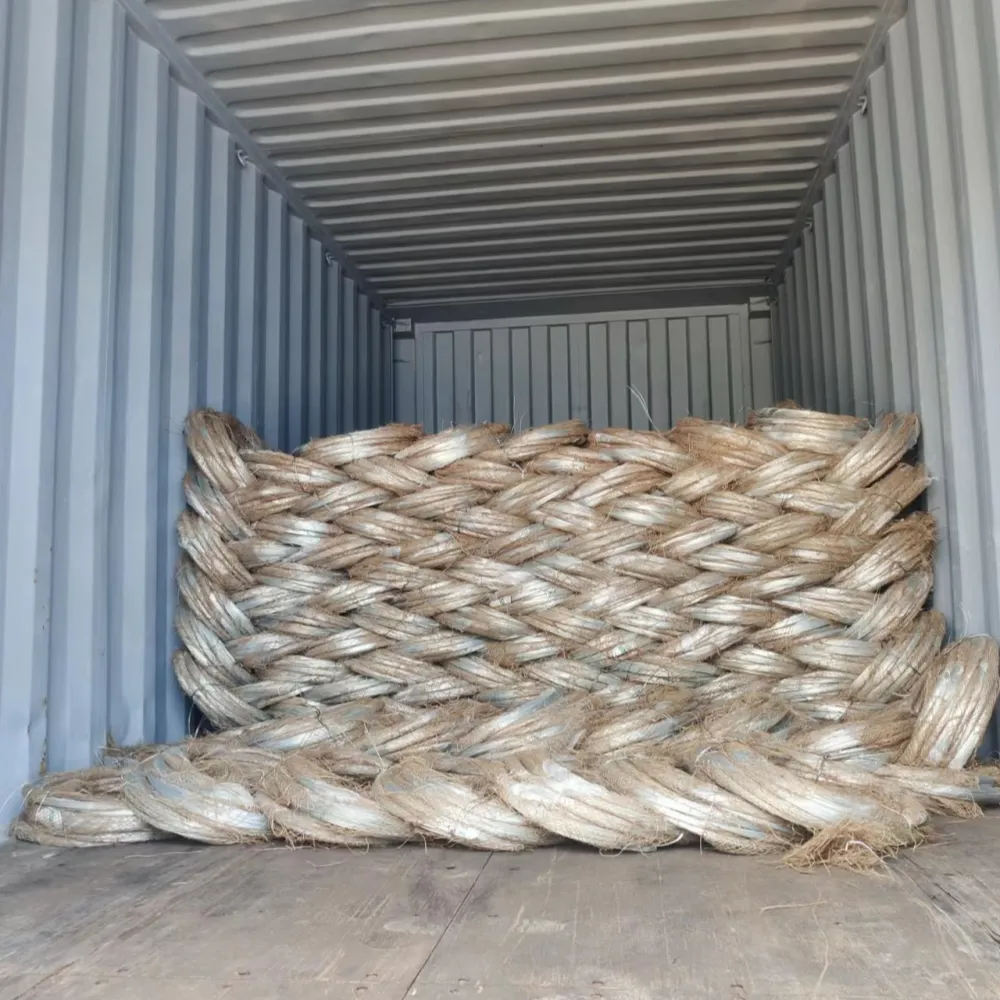
Another crucial factor is the mesh opening size, which influences its functional performance. The openings can vary significantly, from small sizes meant to reinforce minor concrete sections to larger openings used for fencing solutions. Standard sizes range from 1/4 inch to several inches square. Depending on application needs, selecting the appropriate opening size helps optimize material use and project success.
Material composition is also paramount in welded wire mesh specs. Common materials include galvanized steel, stainless steel, and PVC-coated wire, each offering unique advantages. Galvanized wire mesh provides outstanding corrosion resistance and is ideal for outdoor use. Stainless steel mesh offers superior strength and resistance to extreme temperatures, making it suitable for demanding environments. PVC-coated mesh offers additional protection against the elements, enhancing durability and longevity.
welded wire mesh specs
The welding method used to produce the mesh significantly impacts its performance characteristics. Automated welding ensures precision and uniformity across the entire mesh structure. This uniformity is essential for maintaining consistent strength and stability across all areas, making it reliable under various stresses. Manual welding, though less common, can offer custom solutions for specialized applications that require tailored specifications.
Quality certification is an additional measure of the authoritative nature of welded wire mesh. When purchasing, it’s vital to look for products that meet or exceed industry standards such as ASTM (American Society for Testing and Materials) or ISO (International Organization for Standardization) certifications. These specifications ensure the mesh has been manufactured to rigorous quality standards and will perform reliably under specified conditions.
Understanding the practical applications of welded wire mesh is also integral to leveraging its full benefits. It is prominently used in reinforcing slabs and walls, contributing to increased stability and reduced cracking. Additionally, it serves an essential role in constructing cages, partitions, grates, and enclosures due to its robust and flexible nature. Industrial projects frequently incorporate welded wire mesh in conveyor belts and machine guards, where its strength and safety assurance are highly valued.
Sourcing welded wire mesh from reputable suppliers significantly impacts the end result of a project. Trusted suppliers often provide comprehensive product documentation, along with technical support, to guide appropriate usage and specification understanding. Establishing long-term relationships with these suppliers can enhance project efficiency and product appropriateness, contributing to overall success.
In conclusion, the specific attributes of welded wire mesh, such as wire gauge, mesh opening size, material choice, and welding method, all play pivotal roles in determining the most suitable product for any given project. Combining quality certifications and reliable suppliers with a clear understanding of welded wire mesh specs will ensure products meet stringent demands and contribute to project longevity and success. Investing in the right specifications can ultimately offer enhanced safety, performance, and cost-effectiveness, affirming the enduring value of this versatile material.