Welded wire mesh has become an essential component in various construction, agricultural, and industrial applications. Understanding the weight of welded wire mesh is crucial for making informed decisions about its use, cost, and transportation. This article explores the intricacies of welded wire mesh weight, providing a comprehensive understanding that fosters trust and demonstrates authority in this field.
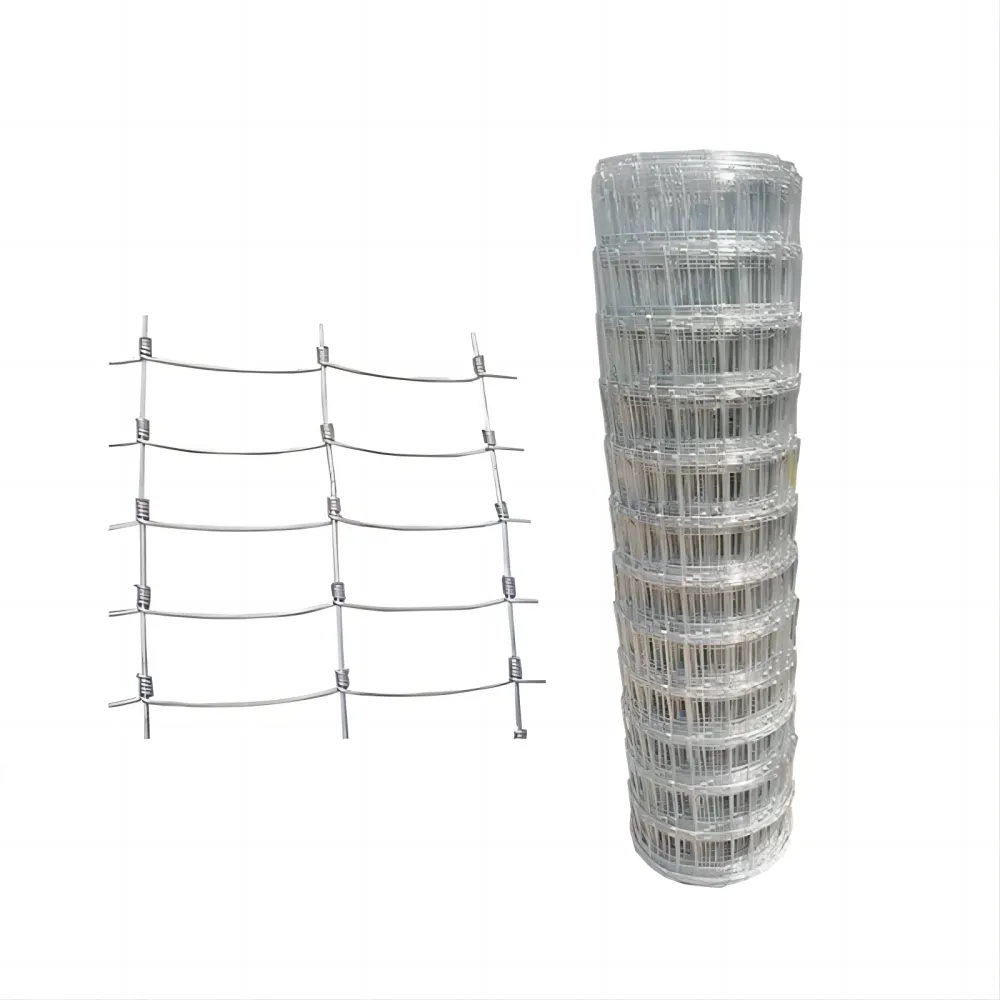
The weight of welded wire mesh is determined by several factors, including wire diameter, mesh size, and the material from which it is made. Predominantly manufactured from steel, galvanized steel, or stainless steel, each material variant offers unique benefits and weight considerations.
Wire diameter plays a significant role in determining the overall weight of the mesh. Thicker wires mean increased weight, which translates to enhanced strength and durability. However, choosing the appropriate wire diameter involves a delicate balance; while thicker wires provide greater support and longevity for structural applications, they also increase the overall weight, affecting transportation costs and ease of installation. For example, in industrial settings that require heavy-duty support, wire diameters ranging from 4mm to 6mm are commonly utilized. These ensure structural integrity, particularly in high-stress environments.
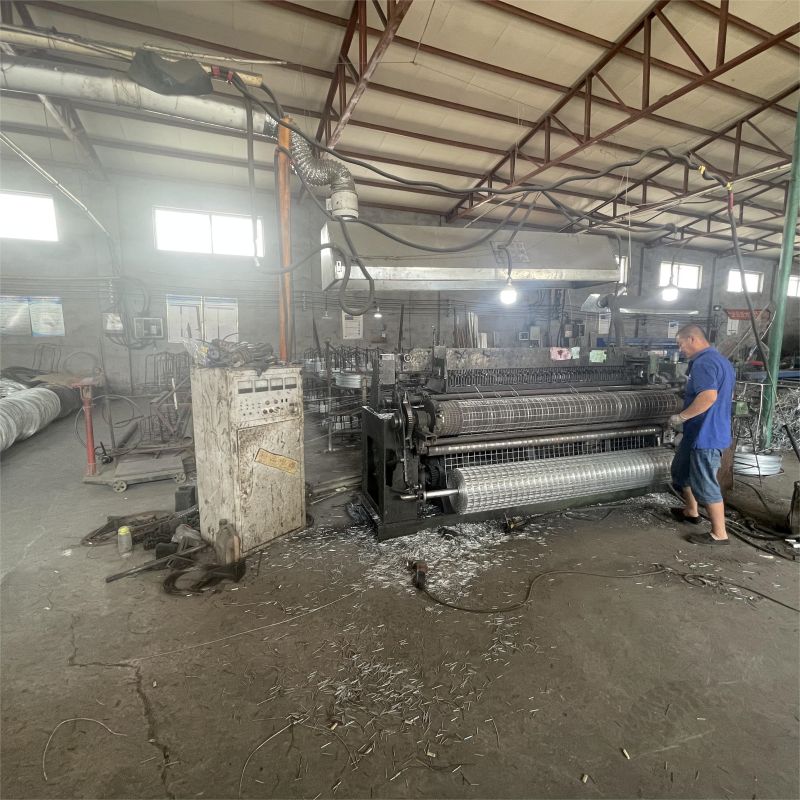
Mesh size, defined by the number of grid openings per square inch, also impacts the weight. A smaller mesh size with more frequent intersections results in a heavier material. This is crucial for contexts that require high load-bearing capabilities, such as reinforced concrete slabs or security fencing. Conversely, lighter mesh with a larger grid may suffice for applications that prioritize coverage and visual barriers, such as pedestrian safety railings or agricultural enclosures.
Material selection further influences the welded wire mesh's weight. Galvanized steel is favored for its balance of durability and corrosion resistance, making it suitable for outdoor applications like fencing where exposure to the elements is a concern. In contrast, stainless steel, though heavier, offers unmatched corrosion resistance for use in highly corrosive environments, such as marine or chemical facilities.
welded wire mesh weight
Identifying the right welded wire mesh involves assessing the specific requirements of your project—load-bearing needs, environmental conditions, and budget constraints. Professional guidance and comprehensive analysis of project specifications are recommended; consulting with structural engineers or experienced suppliers can yield invaluable insights into selecting the optimal wire diameter, mesh size, and material combination.
From a logistical perspective, understanding and calculating the weight of welded wire mesh is vital for planning shipment methods and site handling processes. Heavy gauge welded wire typically requires heavy-duty equipment for transport and installation. Working closely with logistics providers ensures that the transportation of such materials is managed efficiently, reducing the risk of delays and potential damage.
In summary, welded wire mesh weight is a critical factor influencing its selection and application across various industries. The right combination of wire diameter, mesh size, and material can optimize performance and cost across diverse construction and industrial scenarios. By providing this technical knowledge, we enhance our credibility and establish a foundation of trust, ensuring that stakeholders make informed and effective decisions for their mesh-related needs.
For those needing expert advice, engaging with seasoned professionals in the field can significantly streamline the decision-making process. Armed with this understanding, professionals can confidently specify the most appropriate welded wire mesh, thereby optimizing performance and ensuring long-term satisfaction with their investments.