Wire cloth, also known as wire mesh or wire fabric, plays an integral role in a multitude of industrial and commercial applications. Recognized for its versatility and durability, wire cloth is a preferred choice for manufacturers and engineers alike. This article delves into the significance of wire cloth, examining its applications, manufacturing processes, and the qualities that make it an indispensable resource.
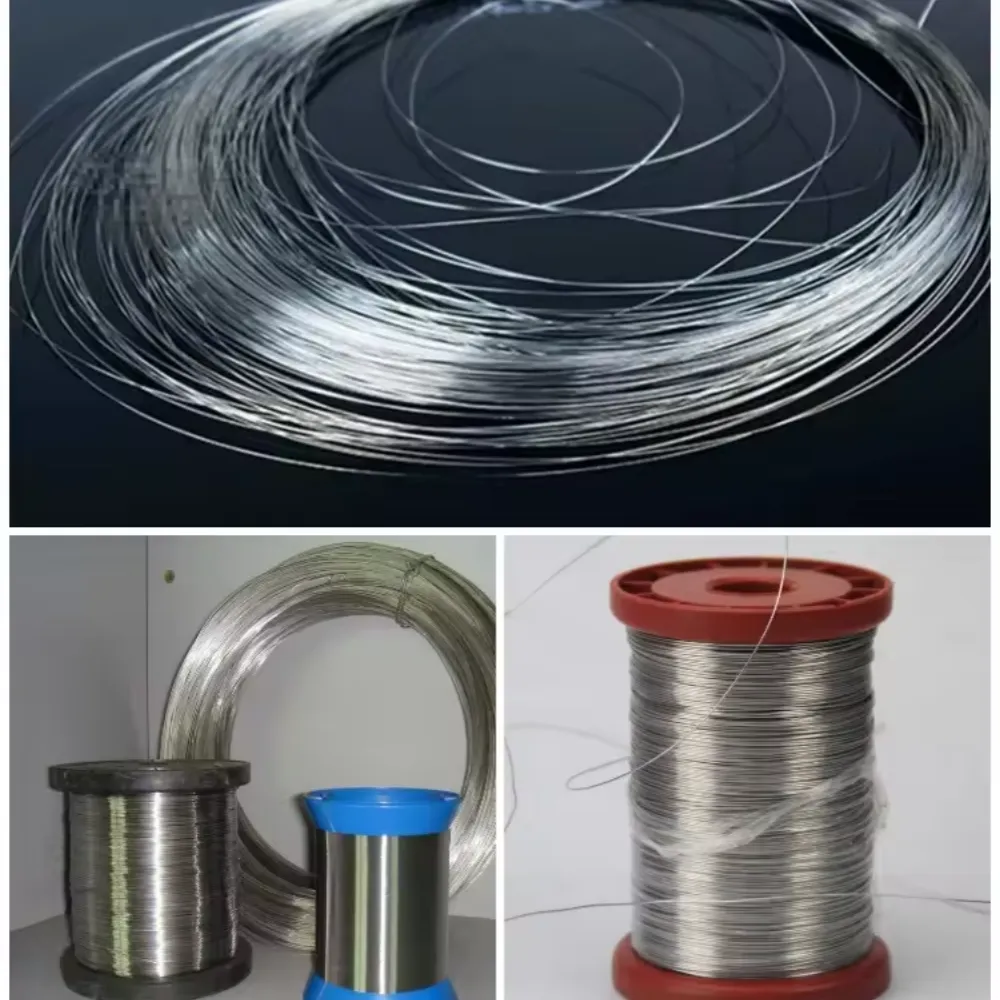
Wire cloth's utility transcends numerous industries owing to its customization options in terms of material, weave, and configuration. Typically fabricated from materials like stainless steel, brass, copper, and aluminum, the choice of material often hinges on the intended application. Stainless steel, renowned for its strength and resistance to corrosion, is favored in industries where durability is paramount. In contrast, copper and brass are selected for their conductivity and resistance to atmospheric corrosion, making them suitable for specific electrical or decorative applications.
The manufacturing process of wire cloth is a meticulous endeavor that requires precision and expertise. Initially,
raw metal wire is drawn to the desired diameter. The weaving process then commences, where these wires are interlaced to create distinct patterns. The most common weave patterns include plain, twill, and Dutch weaves. Each weaving style confers unique properties to the wire cloth; for instance, a plain weave offers a balance between strength and flexibility, while a Dutch pattern enhances filtration capabilities by having more weft than warp wires.
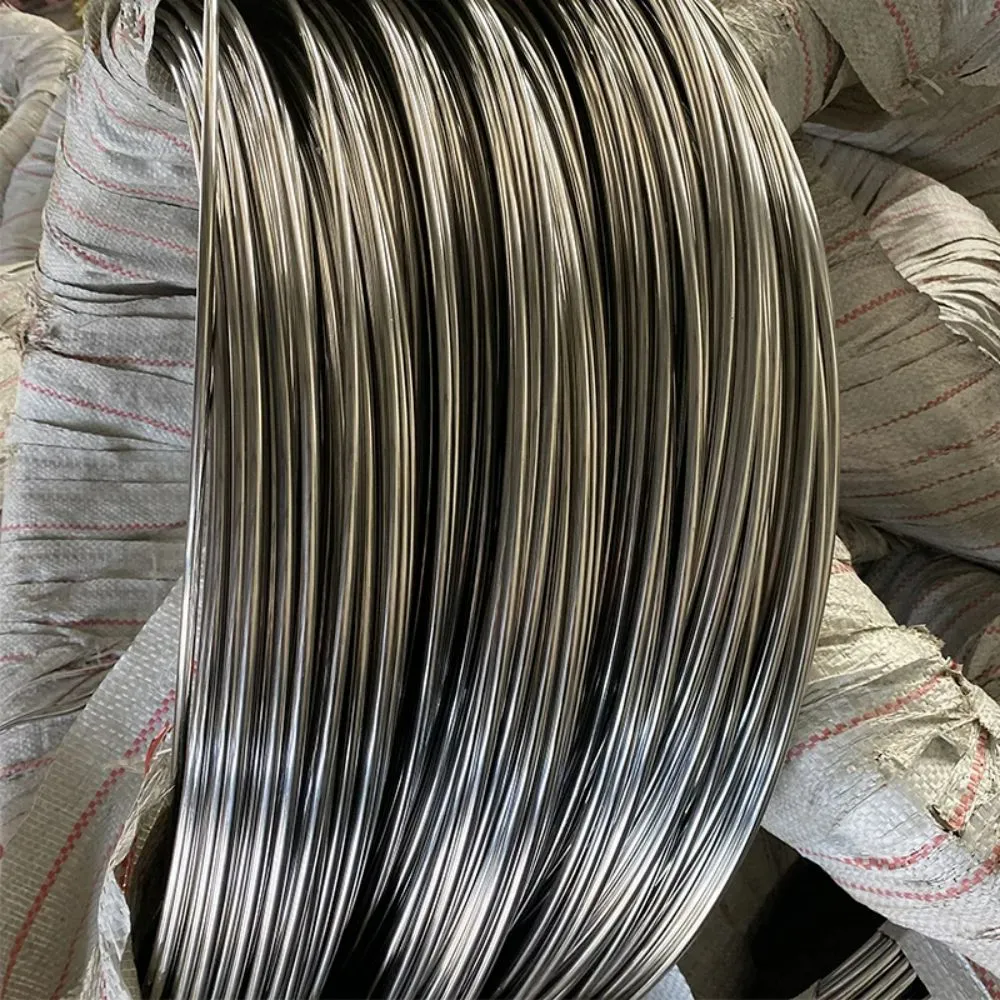
Wire cloth's adaptability is evidenced by its diversified applications. In the industrial sector, it serves as a key component in filtration systems, sieves, screens, and conveyor belts. The precision and uniformity of wire cloth make it ideal for filtering out particulates in liquids and powders. In the architectural realm, wire cloth provides both aesthetic appeal and functional benefits, being used in building facades, balustrades, and interior design elements that demand a modern industrial look.
Moreover, in the realm of safety, wire cloth serves as a protective barrier. In chemical plants and refinery operations, it is used in the construction of protective grilles and ventilation screens that prevent foreign objects from entering machinery, thereby ensuring operational safety. The robustness of wire cloth makes it a suitable material for constructing partitions and cages that require strong yet breathable walls.
wire cloth
Wire cloth's unique attributes encompass not just physical durability but also an ability to withstand extreme conditions. Its resistance to heat and corrosion enables usage in challenging environments such as petrochemical processes and high-temperature manufacturing. Furthermore, its light weight relative to strength ratio provides an advantage in applications where both these traits are crucial.
For businesses seeking quality wire cloth, selecting a trustworthy supplier is paramount. A reputable manufacturer provides not only a range of customizable options but also adherence to industry standards and quality assurances. Certifications such as ISO compliance indicate a commitment to maintaining rigorous production processes and quality control mechanisms.
In addition, innovative technological advancements are enhancing the capabilities of wire cloth. Modern computer-aided design (CAD) software allows manufacturers to produce intricate patterns and custom configurations with high precision. This technological integration ensures that wire cloth can meet the specific demands of various industries, from complex architectural designs to specialized filtration systems.
As industries evolve, the demand for high-quality and versatile materials like wire cloth remains steadfast. Its application in enhancing manufacturing efficiency, promoting safety, and supporting dynamic industrial processes underscores its importance. As such, wire cloth not only upholds its legacy as a multifunctional industrial asset but also continues to pave the way for future innovations in material applications. As manufacturers and engineers seek to address contemporary and future challenges, wire cloth's adaptability, reliability, and strength assure its place as an indispensable component across numerous landscapes.