Choosing between woven and welded wire mesh can be a daunting task, given the multifaceted applications and the technicalities involved in each option. Both types of wire mesh have unique qualities making them suitable for different projects and industries. Here is an in-depth analysis of woven versus welded wire mesh, aimed at guiding you with expertise and authority, ultimately ensuring a trustworthy decision-making process.
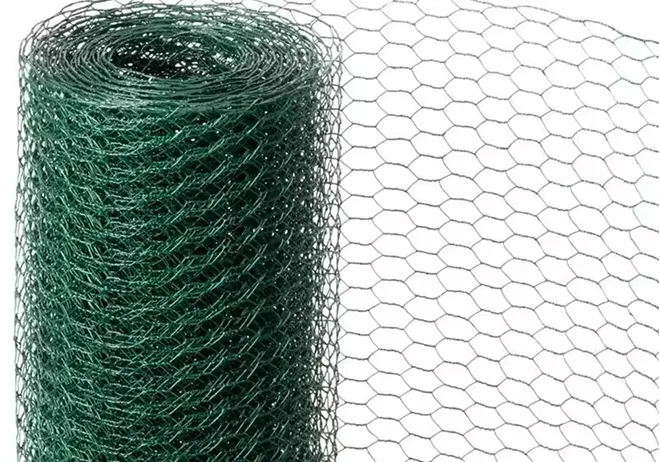
Woven wire mesh is crafted through the interweaving of metal wires, similar to how fabric is made. This method allows for flexibility and versatility in its uses, making it ideal for applications that require a durable yet adaptable material. The interlaced construction of woven wire mesh means it can better sustain impact loads without deformation, making it particularly beneficial for industrial sieving, filtration processes, and architectural designs where aesthetic appeal is as crucial as functionality.
Professionals often select woven mesh for scenarios demanding precision and finer filtration. The meticulous intertwining of each wire provides consistent openings and maintains a precise apertures size, vital for industries such as pharmaceuticals and food processing, where contamination is non-negotiable. Moreover, its superior elasticity compared to welded mesh allows for installations that might require shaping around uneven surfaces without compromising the structural integrity of the mesh.
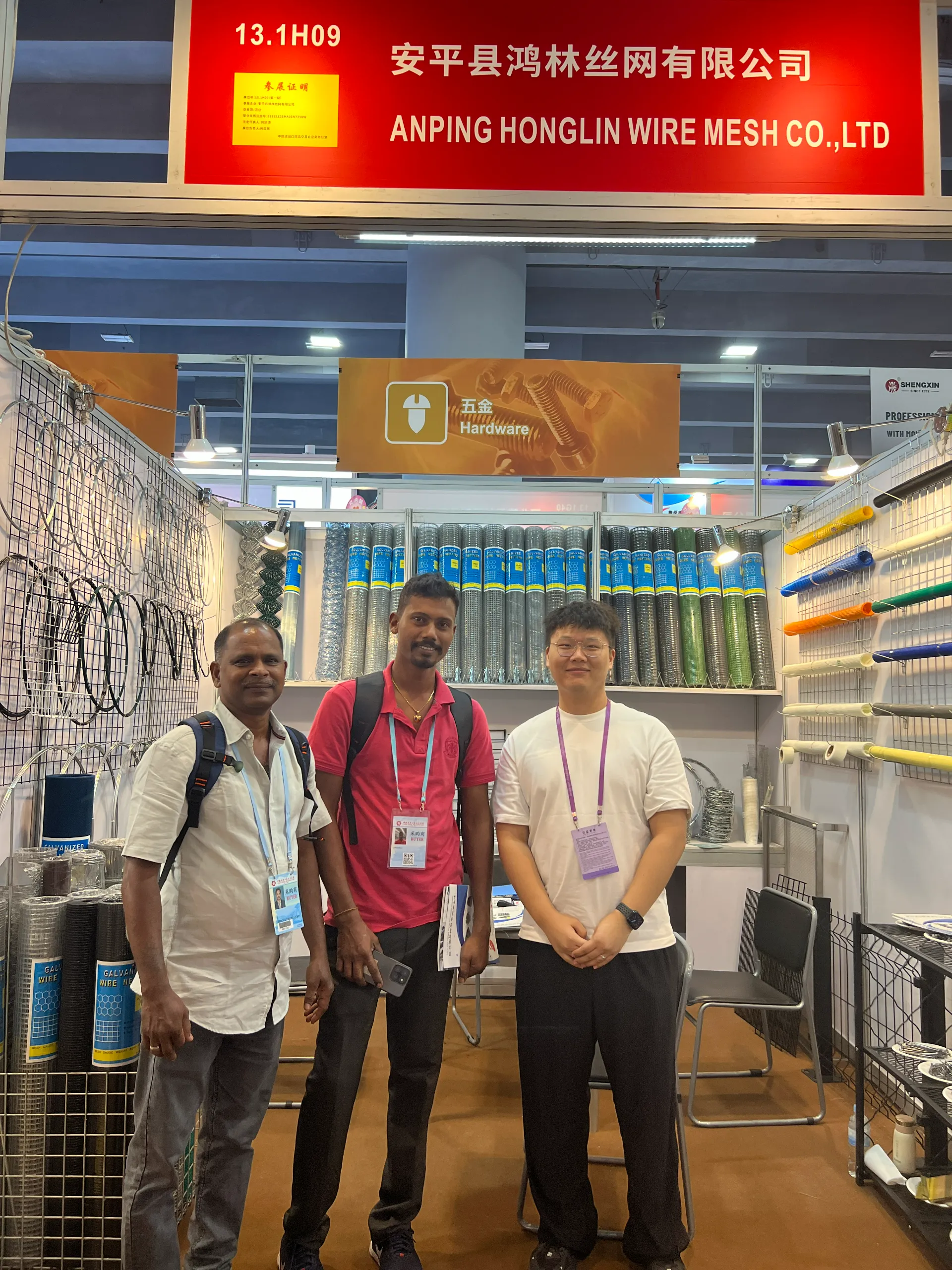
On the other hand, welded wire mesh is formed by fusing intersecting wires at their junctions through a sophisticated welding process. This manufacturing style offers a robust and rigid product, characterized by its capability to uphold heavy loads and maintain its form under stress. Because of these attributes, welded wire mesh is frequently utilized in construction, agriculture, and security applications—think reinforcement in concrete, animal enclosures, and fencing systems.
One significant advantage of welded wire mesh is its ease of installation and cutting, which translates to time savings and labor cost reductions on site. The rigidity of the joints prevents unraveling, making it a dependable choice for permanent installations requiring longevity and durability. However, the welding process, although enhancing strength, makes it less suitable for scenarios where the mesh needs to be forged into different shapes post-production.
woven vs welded wire mesh
Both woven and welded wire meshes are available in a variety of metals including stainless steel, galvanized steel, and aluminum, affecting their corrosion resistance and suitability for different environments. Mild steel welded mesh, for instance, gains preference in structures that need additional strength but aren't exposed to corrosive elements, while stainless steel woven mesh fits perfectly in highly corrosive settings due to its excellent oxidation resistance.
Understanding the environmental factors is crucial when selecting between these two. Woven wire mesh, with its flexible structure, tends to perform better in areas of high vibration or movement, reducing the chances of snapping under pressure. Conversely, for static applications where strength supersedes flexibility,
welded wire mesh becomes the superior choice.
Costing is another pivotal element influencing decision-making. Typically, woven wire mesh can be more expensive than its welded counterpart due to the intricacies of its creation process. However, the investment often outweighs the expanse in highly specialized applications requiring its distinctive properties. Welded mesh offers a cost-effective solution for larger scale, high-strength projects without the necessity for fine precision.
In conclusion, the decision between woven and welded wire mesh should be rooted in a comprehensive understanding of the application's specific needs, considering factors such as flexibility versus rigidity, installation conditions, environmental exposures, and budget constraints. Consulting with industry experts and thoroughly analyzing the demands of your project ensures a reliable choice that upholds Experience, Expertise, Authoritativeness, and Trustworthiness—the four cornerstones of a successful and sustainable solution.